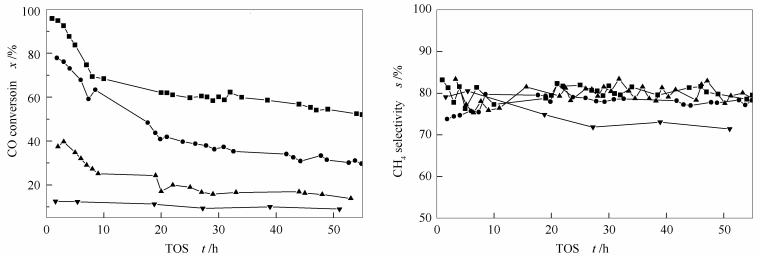

Citation: WANG Hui, ZHANG Jun-feng, BAI Yun-xing, WANG Wen-feng, TAN Yi-sheng, HAN Yi-zhuo. NiO@SiO2 core-shell catalyst for low-temperature methanation of syngas in slurry reactor[J]. Journal of Fuel Chemistry and Technology, 2016, 44(5): 548-556.

NiO@SiO2核壳催化剂在浆态床中低温甲烷化研究
English
NiO@SiO2 core-shell catalyst for low-temperature methanation of syngas in slurry reactor
-
Key words:
- core-shell
- / nickel-based catalyst
- / slurry reactor
- / low-temperature methanation
-
天然气是一种清洁、安全、高效的优质能源,随着中国经济的快速发展,天然气的需求急剧增长。中国能源结构的特点是“富煤、贫油、少气”。因此,发展以煤基合成气和焦炉煤气为原料生产替代天然气(SNG) 的技术,对于缓解中国天然气供需矛盾具有重要意义[1]。甲烷化反应是一个强放热反应,如何将甲烷化反应过程中放出的大量热及时转移是目前甲烷化发展面临的一个难题。目前,甲烷化工业过程普遍采用以固定床反应器为核心的甲烷化工艺,反应温度较高,极易造成催化剂床层局部过热,引起催化剂烧结和积炭,进而导致失活。与传统的固定床反应器相比,浆态床反应器以惰性液体为反应介质,可以将反应过程中产生的大量热快速转移,同时具备催化剂可在线更换、反应系统热稳定性高和易实现恒温操作等优点,另外浆态床反应温度相对较低,有利于提高CO平衡转化率并避免催化剂烧结与积炭[2]。因此,在浆态床中进行甲烷化反应是一条非常有潜力的工艺路线。
目前,部分科研人员开展了浆态床低温甲烷化的研究,已取得了一定进展[2-7]。而在浆态床中进行的低温甲烷化研究大多集中于对负载型催化剂制备方法或反应工艺条件改善等方面的考察,相关催化剂虽显示出较好活性,但在高空速下失活较为严重。Zhang等[4]对浆态床中催化剂的失活行为已做了较深入的研究,发现在低温浆态床中,传统的负载型Ni基催化剂的失活主要是由于活性组分Ni与合成气中的CO作用,形成易于在催化剂表面自由迁移的羰基镍物种(Ni (CO)x(x=1-4)),导致Ni颗粒聚集长大,从而引起催化剂失活。在合成气低温甲烷化过程中,负载型Ni基催化剂上Ni (CO)x的生成难以避免。因此,设计并制备一种新型结构的催化剂,减少和抑制Ni (CO)x物种在催化剂表面的迁移,从而提高其稳定性,将是开展浆态床中低温甲烷化研究的重点内容之一。
近年来,核壳结构催化剂由于其自身的特殊结构而受到广泛的关注。核壳结构催化剂中研究较多的为硅基核壳结构催化剂,即由SiO2包覆的复合型催化剂。硅基核壳结构催化剂的制备多采用改性的Stöber方法[8],例如, Yao等[9]通过添加偶联剂,使金属氧化物纳米粒子能够相对稳定地存在于醇水体系中,然后再以正硅酸乙酯(TEOS) 为硅源,水解完成对纳米粒子的包覆。核壳结构催化剂由于其金属活性纳米粒子受到外壳层的保护,在一些过渡金属催化的反应中,尤其是高温反应,如甲烷重整[10-15]、氨分解制氢[16]等,金属活性纳米粒子的长大将受到极大的限制,从而使其保持良好的反应活性和稳定性;另外,通过对核壳催化剂壳层孔道、厚度等性质的调控,可以提高目标产物的选择性,如核壳催化剂在费托合成[17-20]中的研究。Li等[21]制备了一种NiO-MgO@SiO2核壳结构催化剂,并在微型固定反应器中进行CO2低温甲烷化反应,发现核壳结构催化剂在连续反应100 h内,CO2转化率基本保持不变。鉴于合成气低温甲烷化反应中催化剂存在由Ni (CO)x生成、迁移和聚集所导致的失活问题,为限制Ni (CO)x的迁移和聚集,实验制备了一种由SiO2包覆的核壳结构催化剂(NiO@SiO2),在浆态床反应器上考察其甲烷化反应行为,并结合反应前后催化剂的表征结果,探讨了核壳催化剂形貌变化与其反应行为之间的内在关系。
1 实验部分
1.1 催化剂的制备
镍基核壳结构催化剂的制备分两步进行,即NiO纳米颗粒的制备和NiO纳米颗粒的包覆,具体方法如下。
NiO纳米颗粒的制备:称取29.1 g Ni (NO3)2·6H2O溶解于400 mL水中,取3.3 g聚乙二醇(PEG-20000) 和10.0 g NaOH溶解于1 000 mL水中。在搅拌条件下,通过蠕动泵在100 min内将Ni (NO3)2溶液滴加到NaOH溶液中。静置老化1 h,沉淀经离心、乙醇洗涤后,置于干燥箱中50 ℃干燥10 h。干燥后的样品研磨至300目,分别经350、400和500 ℃焙烧2 h,所得样品分别命名为NiO-350、NiO-400和NiO-500。
NiO纳米颗粒的包覆:取1.0 g NiO和10.0 g聚乙烯吡咯烷酮(PVP-K30),分散于1 000 mL无水乙醇中,搅拌12 h。加入100 mL NH3·H2O (25%),超声30 min。然后,加入TEOS溶液(1.0 mL TEOS,50 mL乙醇),在超声条件下反应1.5 h。产物经乙醇洗涤,离心回收后,于70 ℃干燥5 h,500 ℃焙烧3 h。包覆后样品分别命名为NiO-350@SiO2、NiO-400@SiO2和NiO-500@SiO2。
NiO-500/SiO2催化剂的制备:分别取0.4 g SiO2(20 nm) 和1.5 g NiO-500,充分研磨20 min。
1.2 催化剂的活性评价
催化剂评价在浆态床中进行,反应器体积为250 mL,液体石蜡(80 mL,馏出温度高于340 ℃) 为反应介质[4]。具体操作为:取1.0 g催化剂置于石英舟后,放入水平的石英管中,在流量为30 mL/min的H2流下,升温至450 ℃,保持3 h,然后自然冷却至室温。为防止催化剂被重新氧化,向石英舟中加入一定量的石蜡,再将催化剂转移至反应釜中。随后在氮气保护下,升温至320 ℃,而后通入合成气(H2:CO体积比为3:1) 进行反应。反应压力为1.5 MPa,搅拌转速为1 000 r/min,空速(WHSV) 为10 000 mL/(g·h),尾气分别用TCD和FID检测器的气相色谱进行分析,并用湿式流量计测定尾气累积体积变化。CO转化率(xCO) 和产物选择性(si) 由以下公式计算得到:
式中,nCO, in为原料气中CO的摩尔数; nCO, out为尾气中CO的摩尔数; ni, out为尾气中产物i的摩尔数。
1.3 催化剂的表征
XRD测试在德国Bruker公司D8 Advance型X射线衍射仪上进行,Cu Kα为射线源,扫描速率为4(°)/min,20°-90°扫描。催化剂的形貌在日立JEM-1011型透射显微镜下观察,加速电压80 kV。催化剂体相组成通过TJA公司的Atom scan 16型ICP-AES谱仪获得。催化剂表面组成在Kratos公司AXIS ULTRA DLD型X射线光电子能谱仪上进行(XPS),单色化Al靶为射线源,表征样品分别取自催化剂在反应前(未经还原) 和反应后(石油醚洗涤并干燥) 的样品。在Tristar 3020自动吸附仪上测定催化剂的比表面积、孔体积和孔径,催化剂在200 ℃下脱气预处理。
2 结果与讨论
2.1 催化剂活性评价
图 1为制备的三种核壳催化剂(NiO-350@SiO2、NiO-400@SiO2和NiO-500@SiO2) 及NiO-500/SiO2催化剂上,合成气甲烷化活性随反应时间的变化。由图 1可知,NiO-350@SiO2和NiO-400@SiO2的初始CO转化率分别为96%和80%,而NiO-500@SiO2的初始CO转化率仅有40%,而且随着反应时间的延长,三种核壳催化剂的CO转化率均呈现下降趋势。由文献可知[14], 在制备NiO纳米粒子的过程中,颗粒粒径会随焙烧温度的升高而增加。从图 1中可以看出,催化剂的活性会随着核颗粒粒径的增大而明显降低。在反应起始的前20 h内,催化剂均出现快速失活。反应20 h后,三种核壳催化剂上CO转化率的下降速率明显减慢。而由机械混合得到的NiO-500/SiO2催化剂明显比核壳型NiO-500@SiO2催化剂的CO转化率低,且随着反应进行而出现失活,这说明NiO-500颗粒的包覆对其甲烷化活性具有重要的影响。另外,作者在实验中也对未包覆NiO-500纳米颗粒(评价结果在图 1中未列出) 进行了活性评价,结果显示,NiO-500纳米粒子在反应初期有极其微弱的甲烷化活性,在反应2 h后几乎没有任何活性,这进一步表明催化剂的核壳结构对其甲烷化性能有明显的提高。由图 1还可知,三种核壳催化剂上,CH4选择性基本维持在80%左右,而NiO-500/SiO2催化剂的CH4选择性随着反应的进行出现了一定的下降。
图 1 不同催化剂的反应性能 Figure 1. CO conversions and CH4 selectivities as a function of time on stream over the different catalysts
2.2 催化剂的表征
2.2.3 XPS表征
为进一步了解反应后催化剂表面元素组成的变化,分别对反应前后的催化剂进行了XPS表征。图 5为反应前后NiO@SiO2催化剂Ni元素的XPS谱图。在Ni 2p图中,未还原的反应前样品在856.1 eV处出现明显的峰,可归属为Ni2+ 2p3/2。反应后的样品在853-858 eV出现两个峰,结合能较低的为Ni0 2p3/2的峰,较高的为Ni2+ 2p3/2的峰,表明反应后的样品在提取和测试过程中Ni核颗粒存在部分氧化。通过对反应前后三种催化剂的XPS谱图的积分计算,可以得出催化剂表面组分的原子浓度,见表 2。由表 2可知,反应前三种催化剂的表面Ni原子浓度均明显低于体相理论Ni含量,这是因为XPS测试中,X射线只能探测到催化剂的近表面区域(5 nm左右),NiO颗粒被SiO2包裹后,X光电子束难以全部穿透较厚的壳层激发内部的NiO核颗粒,XPS信号主要来源于催化剂中存在少量未包覆的NiO颗粒以及包覆相对较薄的区域。
随着Ni核粒径的增加,催化剂的表面Ni原子浓度明显下降,一方面, 是因为核颗粒越大,其包覆的壳层越厚,催化剂中存在的包覆相对较薄的区域会明显减少;另一方面, 是由于催化剂中未包覆的NiO颗粒也会随着核颗粒粒径的增大而明显减少。对比同一催化剂在反应前后的表面Ni/Si原子比,可以发现,反应后NiO-400@SiO2和NiO-500@SiO2的表面Ni/Si原子比均出现了明显的下降,这是因为催化剂中含有少量未包覆的和包覆较薄的NiO颗粒,相对于包覆较厚的Ni颗粒而言,这一部分Ni颗粒在形成Ni (CO)x后更容易发生迁移,Ni (CO)x在由壳外或者从包覆较薄的壳层内迁移到较厚的壳层内后发生聚集,使Ni核发生长大,从而导致XPS所测的催化剂表面Ni/Si原子比降低。XPS的结果也说明未包覆的壳外Ni颗粒所形成的Ni (CO)x或者从包覆不够完美的核壳内迁移出的Ni (CO)x并没有在壳外富集或分解,这也进一步验证了上文有关Ni (CO)x迁移规律的推断。而NiO-350@SiO2的壳层平均厚度只有6.1 nm,X光电子束容易穿透壳层进而激发内部的Ni颗粒,所以Ni颗粒迁移或长大对其表面Ni/Si原子比的影响并不明显。
2.2.2 TEM表征
图 3为三种不同NiO纳米颗粒在包覆前((a)、(b)、(c)) 及包覆后((d)、(e)、(f)) 的TEM照片和粒径分布。由图 3(a)-3(c)可知,Ni (OH)2前驱体经不同温度焙烧处理后,能够得到近似于球形的NiO纳米颗粒,并且随着焙烧温度的升高,颗粒之间发生团聚,造成颗粒长大、粒径分布变宽。根据统计结果(表 1),NiO-350、NiO-400、NiO-500样品的平均颗粒粒径分别为4.9、8.1、23.7 nm,这与XRD计算的晶粒粒径结果基本保持一致。结合核壳催化剂的评价结果可以看出,催化剂的甲烷化活性依赖于Ni核的平均粒径,随着核颗粒粒径的增大,催化剂的活性发生了明显下降。在反应起始10 h内,NiO-350@SiO2的失活速率较快,NiO-500@SiO2的失活速率次之,而NiO-400@SiO2的失活速率最慢。这是由于核颗粒粒径越小,其表面能越高,Ni核易发生聚集长大,导致NiO-350@SiO2的失活速率较高;相反,NiO-500@SiO2的核颗粒较大,失活速率较低;而根据Peter等[22]的研究,颗粒粒径为8-10 nm的Ni颗粒在CO气氛下能够相对稳定的存在,所以核颗粒平均粒径为8.1 nm的NiO-400@SiO2样品在反应起始的10 h内表现出比另外两种样品更慢的失活速率。然而,在反应10 h后,可能由于催化剂结构遭到破坏,三种催化剂的失活行为趋于一致,催化剂均表现出均匀缓慢地失活。
表 1 NiO颗粒粒径及反应前后NiO@SiO2的核壳尺寸 Table 1. Particle size of NiO, core size and shell thickness of NiO@SiO2
Sample Core d/nm Shell d/nm NiO-350 4.9 - NiO-350@SiO2 5.1 6.1 Used NiO-350@SiO2 8.1 5.0 NiO-400 8.1 - NiO-400@SiO2 8.6 11.2 Used NiO-400@SiO2 10.6 10.1 NiO-500 23.7 - NiO-500@SiO2 23.3 23.0 Used NiO-500@SiO2 27.8 20.6 表 1 NiO颗粒粒径及反应前后NiO@SiO2的核壳尺寸
Table 1. Particle size of NiO, core size and shell thickness of NiO@SiO2实验中采用改进的Stöber方法对NiO颗粒进行了包覆,包覆后颗粒见图 3(d)-3(f)。由3(d)-3(f)可知,NiO颗粒被无定形SiO2均匀包覆,核壳结构粒子的壳层出现相互黏结的现象,这是TEOS水解后形成的Si-OH容易发生交联所致[17]。另外,对于小于10 nm的NiO-350和NiO-400纳米颗粒,会出现多核包覆的现象,而且包覆后的样品存在少量未包覆的NiO颗粒;而NiO-500在包覆后基本都显示出单核包覆的形貌,且NiO-500@SiO2样品中几乎不存在未包覆的NiO纳米颗粒,这说明核颗粒的粒径会直接影响纳米粒子的包覆效果。根据表 1的统计结果,NiO-350@SiO2、NiO-400@SiO2和NiO-500@SiO2的核颗粒平均粒径分别为5.1、8.6和23.3 nm,壳层平均厚度依次为6.1、11.2、23.0 nm。由表 1可以看出,在相同的制备条件下,随着核颗粒的增大,其壳层厚度也相应增加。NiO经包覆、焙烧处理后,其平均颗粒粒径基本保持不变,说明SiO2壳层对NiO核起到了保护作用,有效抑制了焙烧过程中NiO核颗粒的长大。
图 4为反应后核壳催化剂(used NiO-350@SiO2、used NiO-400@SiO2和used NiO-500@SiO2) 的TEM照片。由图 4可知,反应后不同催化剂的Ni核颗粒均出现了一定程度的长大。三种催化剂中核颗粒的粒径分别增大至8.1、10.6和27.8 nm,而壳层厚度分别为5.0、10.1、20.6 nm (见表 1)。这表明,反应过程中合成气对核颗粒粒径的影响较大,而对壳层厚度几乎没有影响。此外,从TEM照片中还观察到,反应后部分催化剂的Ni核消失,出现了SiO2空壳(如图 4(a)-4(c)中圆圈内所示),这表明Ni核在CO的作用下迁移出了壳层。然而,在TEM照片中并未能观察到壳外存在明显的未包覆Ni颗粒。而ICP的分析结果(见表 2) 又表明, 催化剂在反应前后的Ni含量均为62%左右,没有发生明显的流失。在低温甲烷化条件下,Ni与CO作用生成Ni (CO)x物种的中间过程是难以避免的[23],结合核颗粒在反应后发生长大的事实,推测催化剂形貌变化可能的过程为:一部分包覆效果不太完美或者具有较小核颗粒的核壳结构很容易与CO作用,形成Ni (CO)x而迁移至壳外,留下了空壳;而这些迁移至壳外的Ni (CO)x物种的浓度较低,难以达到Ni单独成核所需的过饱和度,同时由于在浆态床反应器反混现象的存在,为降低催化剂体系的表面自由能,游离在浆态介质中的Ni (CO)x并未移出反应器,反而会进一步自发地通过核壳催化剂的壳层孔道进入内核,在核壳结构中较大的也即表面自由能相对较低的Ni核上富集、分解,最终导致这一部分核壳结构粒子的核颗粒发生长大,这一过程遵循Ostwald ripening机制;另外,由于存在多核包覆的现象,在反应过程中,同一壳层内的多个Ni颗粒形成Ni (CO)x后在壳层内部迁移聚集,很容易导致壳内Ni颗粒的长大。Li等[13]发现,NiO@SiO2催化剂经还原后会在核与壳之间形成空隙。结合核壳催化剂的评价结果可知,由于壳层内空隙的存在,在反应的前20 h内,Ni核颗粒的长大不受壳层限制,催化剂失活较快;但在反应20 h后,空隙逐渐被长大的Ni核颗粒填满,Ni核自身由于受到壳层的限制,难以进一步发生长大,因而失活速率明显降低。
表 2 反应前后催化剂的表面原子浓度及体相Ni含量 Table 2. Surface atom concentration and Ni content of catalyst before and after reaction
Sample Surface atomic concentrationsa/% Ni/Si
(atomic ratio)Nib/% Ni Si O NiO-350@SiO2 10.11 17.77 72.12 0.57 57.32 Used NiO-350@SiO2 9.85 17.12 73.03 0.58 55.92 NiO-400@SiO2 8.50 24.36 67.14 0.35 58.98 Used NiO-400@SiO2 5.09 27.73 67.18 0.18 61.21 NiO-500@SiO2 6.46 21.22 72.32 0.30 60.68 Used NiO-500@SiO2 4.61 28.38 67.01 0.16 63.14 Theoretical valuec 33.50 11.00 55.50 3.05 62.16 a: the surface atomic concentrations of catalysts were calculated by XPS; b: Ni bulk concentration of catalysts obtained from ICP c: based on the addition mass when catalyst is prepared 表 2 反应前后催化剂的表面原子浓度及体相Ni含量
Table 2. Surface atom concentration and Ni content of catalyst before and after reaction2.2.1 XRD表征
图 2为不同温度焙烧得到的NiO纳米颗粒的XRD谱图。由图 2可知,在37°、43°、63°、75°、79°(JCPDS No.78-0429) 处出现明显的衍射峰,其分别对应于NiO的(111)、(200)、(220)、(311)、(222) 晶面。随着焙烧温度的提高,NiO的特征衍射峰强度逐渐增强,表明NiO晶粒发生聚集长大。根据NiO样品的(200) 晶面处的衍射峰参数,采用Scherrer方程计算了NiO纳米粒子的晶粒粒径,得出三种NiO纳米颗粒的晶粒平均粒径分别为5.0、8.3和21.0 nm。
2.2.4 N2物理吸附表征
图 6为反应前后三种催化剂的N2吸脱附曲线和孔径分布。由图 6(a)可知,反应前的样品均表现出Ⅳ型N2吸脱附等温线,N2吸脱附曲线的吸附线和脱附线之间形成了H1型回滞环,说明三种催化剂的孔径分布较均匀。由于NiO@SiO2的前驱体中残留有一定的偶联剂PVP-K30,PVP-K30也是一种常用的介孔模板剂,所以经过高温焙烧除去PVP-K30后,SiO2壳层中会形成大量孔道[24],形成介孔结构,有利于反应中传质过程的进行。反应后样品呈现出Ⅳ型吸脱附等温线,并出现了H3型回滞环,见图 6(b)。H3型回滞环没有明显的饱和吸附平台,表明孔结构很不规整,这说明反应过程中催化剂的壳层可能发生了结构上的变化。
图 6(c)、图 6(d)分别是反应前和反应后的催化剂孔分布曲线,由图 6(c)、图 6(d)可知,催化剂在3和30 nm左右出现了明显的峰。有关研究[25]认为,催化剂中3-5 nm的介孔是表面活性剂经焙烧去除后形成的介孔,而10 nm以上的孔分布归属为催化剂核壳粒子间的堆积孔。可以发现,反应后催化剂在3-5 nm的介孔明显减少,说明在反应过程中壳层上的介孔被部分破坏,抑制了反应物向活性中心的扩散,这有可能是催化剂在反应20 h后失活的主要原因。表 3为反应前后催化剂的N2吸附,由表 3可以看出,反应后的NiO-350@SiO2和NiO-400@SiO2催化剂的比表面积和孔容均出现明显下降,这可能是壳层上的介孔在反应过程中被破坏所引起。而NiO-500@SiO2的比表面积和孔容的下降相对较小,说明壳层厚度的增加有利于提高壳层孔道的稳定性。
Sample BET surface area A/(m2·g-1) Pore volume v/(cm3·g-1) Pore diameter d/nm NiO-350@SiO2 117.2 0.218 7.4 Used NiO-350@SiO2 52.7 0.147 11.2 NiO-400@SiO2 82.9 0.197 8.2 Used NiO-400@SiO2 43.5 0.101 9.3 NiO-500@SiO2 34.4 0.074 8.6 Used NiO-500@SiO2 23.7 0.073 12.3 表 3 反应前后催化剂的N2吸附
Table 3. N2 sorption of NiO@SiO2 before and after reaction3 结论
通过改进的Stöber方法,可控合成出不同形貌的核壳催化剂NiO-350@SiO2、NiO-400@SiO2和NiO-500@SiO2。制得的催化剂为无定形SiO2均匀包覆的核壳型催化剂,壳层间相互黏结,并出现多核包覆的现象。在相同的制备条件下,核颗粒粒径越大,其包覆的SiO2壳层厚度相应增加,核壳催化剂在焙烧过程中表现出了良好的热稳定性。
在低温浆态床中考察了核壳催化剂形貌对其甲烷化反应性能的影响。随着催化剂核颗粒粒径的增加,催化剂甲烷化活性呈现下降趋势。在反应前20 h内,催化剂出现快速失活,20 h后失活缓慢,催化剂的甲烷选择性都保持在80%左右。在反应过程中,CO会与核壳催化剂壳层内的Ni作用生成易迁移的Ni羰基化物种(Ni (CO)x),这是导致催化剂的核壳结构遭到破坏并出现SiO2空壳的原因。在反应过程中,Ni核颗粒发生长大,壳层中3-5 nm的介孔明显减少,催化剂的比表面积、孔容都出现不同程度的下降,造成了核壳催化剂的失活。
-
-
[1]
张俊峰, 白云星, 张清德, 解红娟, 谭猗生, 韩怡卓. Zr改性Ni/γ-Al2O3催化剂用于浆态相合成气的低温甲烷化[J]. 燃料化学学报, 2013,41,(8): 966-971. ZHANG Jun-feng, BAI Yun-xing, ZHANG Qing-de, XIE Hong-juan, TAN Yi-sheng, HAN Yi-zhuo. Low temperature methanation of syngas in a slurry reactor over Zr-doped Ni/γ-Al2O3 catalyst[J]. J Fuel Chem Technol, 2013, 41(8): 966-971.
-
[2]
孟凡会, 常慧蓉, 李忠. Ni-Mn/Al2O3催化剂在浆态床中CO甲烷化催化性能[J]. 化工学报, 2014,65,(8): 2997-3003. MENG Fan-hui, CHANG Hui-rong, LI Zhong. Catalytic performance of Ni-Mn/Al2O3 catalyst for CO methanation in slurry-bed reactor[J]. CIESC J, 2014, 65(8): 2997-3003.
-
[3]
孟凡会, 刘军, 李忠, 钟朋展, 郑华艳. Ce含量对Ni-Ce/Al2O3催化剂结构及浆态床CO甲烷化性能的影响[J]. 燃料化学学报, 2014,42,(2): 231-237. MENG Fan-hui, LIU Jun, LI Zhong, ZHONG Peng-zhan, ZHENG Hua-yan. Effect of Ce content of Ni-Ce/Al2O3 catalyst constructure and CO methanation in slurry-bed reactor[J]. J Fuel Chem Technol, 2014, 42(2): 231-237.
-
[4]
ZHANG J F, BAI Y X, ZHANG Q D, WANG X X, ZHANG T, TAN Y S, HAN Y Z. Low-temperature methanation of syngas in slurry phase over Zr-doped Ni/γ-Al2O3 catalysts prepared using different methods[J]. Fuel, 2014, 132: 211-218. doi: 10.1016/j.fuel.2014.04.085
-
[5]
黄国宝, 王志青, 李庆峰, 黄戒介, 房倚天. 液相中镍催化剂催化合成气甲烷化的初步研究[J]. 燃料化学学报, 2014,42,(8): 952-957. HUANG Guo-bao, WANG Zhi-qing, LI Qing-feng, HUANG Jie-jie, FANG Yi-tian. Syngas methanation over nickel catalyst in liquid-phase[J]. J Fuel Chem Technol, 2014, 42(8): 952-957.
-
[6]
贺龙.浆态床镍基甲烷化催化剂的研究[D].北京:中国矿业大学(北京), 2012.HE Long. Research of nickel based catalyst for methanation of synthetic gas in slurry bed reactor[D]. Beijing: China University of Mining and Technology (Beijing), 2012.
-
[7]
马胜利.煤基合成气低温甲烷化镍基催化剂的研究[D].太原:中国科学院山西煤炭化学研究所, 2011.MA Sheng-li. Study on low temperature methanation for coal-derived syngas over Ni-based catalyst[D]. Taiyuan: Institute of Coal Chemistry, Chinese Academy of Sciences, 2011.
-
[8]
GRAF C, VOSSEN D L J, IMHOF A, VAN BLAADEREN A. A general method to coat colloidal particles with silica[J]. Langmuir, 2003, 19(17): 6693-6700. doi: 10.1021/la0347859
-
[9]
YAO L H, LI Y X, ZHAO J, JI W J, AU C T. Core-shell structured nanoparticles (M@SiO2, Al2O3, MgO; M=Fe, Co, Ni, Ru) and their application in COx-free H2 production via NH3 decomposition[J]. Catal Today, 2010, 158(3/4): 401-408.
-
[10]
LI Z W, MO L Y, KATHIRASER Y, KAWI S. Yolk-Satellite-Shell Structured Ni-Yolk@Ni@SiO2 Nanocomposite: Superb Catalyst toward Methane CO2 Reforming Reaction[J]. ACS Catal, 2015, 4(5): 1526-1536.
-
[11]
LI Z W, KATHIRASER Y, KAWI S. Facile synthesis of high surface area yolk-shell Ni@Ni embedded SiO2 via Ni phyllosilicate with enhanced performance for CO2 reforming of CH4[J]. ChemCatChem, 2014, 7: 160-168.
-
[12]
LI L, YAO Y, SUN B, FEI Z Y, XIA H, ZHAO J, JI W J, AU C T. Highly active and stable lanthanum-doped core-shell-structured Ni@SiO2 catalysts for the partial oxidation of methane to syngas[J]. ChemCatChem, 2013, 5(12): 3781-3787. doi: 10.1002/cctc.201300537
-
[13]
LI L, HE S C, SONG Y Y, ZHAO J, JI W J, AU C T. Fine-tunable Ni@porous silica core-shell nanocatalysts: Synthesis, characterization, and catalytic properties in partial oxidation of methane to syngas[J]. J Catal, 2012, 288: 54-64. doi: 10.1016/j.jcat.2012.01.004
-
[14]
李雷.核壳结构纳米催化剂的设计与制备及甲烷选择性氧化制合成气研究[D].南京:南京大学, 2012.LI Lei. Core-shell structured nanocatalysts: design, synthesize and their application in partial oxidation of methane to syngas[D]. Nanjing: Nanjing University, 2012.
-
[15]
TAKENAKA S, UMEBAYASHI H, TANABE E, MATSUNE H, KISHIDA M. Specific performance of silica-coated Ni catalysts for the partial oxidation of methane to synthesis gas[J]. J Catal, 2007, 245(2): 392-400. doi: 10.1016/j.jcat.2006.11.005
-
[16]
ZHANG L F, LI M, REN T Z, LIU X Y, YUAN Z Y. Ce-modified Ni nanoparticles encapsulated in SiO2 for COx-free hydrogen production via ammonia decomposition[J]. Int J Hydrogen Energ, 2015, 40(6): 2648-2656. doi: 10.1016/j.ijhydene.2014.12.079
-
[17]
张明伟.核壳结构铁基催化剂的制备及在CO加氢中的应用[D].太原:中国科学院大学山西煤炭化学研究所, 2014.ZHANG Ming-wei. Preparation of core-shell iron-based catalysts and their application for CO hydrogenation[D]. Taiyuan: Institute of Coal Chemistry, Chinese Academy of Sciences, 2011.
-
[18]
ZHANG M W, FANG K G, LIN M G, HOU B, ZHONG L S, ZHU Y, WEI W, SUN Y H. Controlled Fabrication of Iron Oxide/Mesoporous Silica Core-Shell Nanostructures[J]. J Phys Chem C, 2013, 117: 21529-21538. doi: 10.1021/jp4049583
-
[19]
XIE R Y, LI D B, HOU B, WANG J G, JIA L T, SUN Y H. Solvothermally derived Co3O4@m-SiO2 nanocomposites for Fischer-Tropschsynthesis[J]. Catal Commun, 2011, 12(5): 380-383. doi: 10.1016/j.catcom.2010.10.010
-
[20]
XIE R Y, WANG H, GAO P, XIA L, ZHANG Z Z, ZHAO T J, SUN Y H. Core@shell Co3O4@C-m-SiO2 catalysts with inert C modified mesoporous channel for desired middle distillate[J]. Appl Catal A: Gen, 2015, 492: 93-99. doi: 10.1016/j.apcata.2014.12.023
-
[21]
LI Y R, LU G X, MA J T. Highly active and stable nano NiO-MgO catalyst encapsulated by silica with a core-shell structurefor CO2 methanation[J]. RSC Adv, 2014, 4: 17420-17428. doi: 10.1039/c3ra46569a
-
[22]
MUNNIK P, VELTHOEN M E Z, DE JONGH P E, DE JONG K P, GOMMES C J. Nanoparticle growth in supported nickel catalysts during methanation reaction-larger is better[J]. Angew Chem, Int Ed, 2014, 53(36): 9493-9497. doi: 10.1002/anie.201404103
-
[23]
ENGBAEK J, LYTKEN O, NIELSEN J H, CHORKENDORFF L. CO dissociation on Ni: The effect of steps and of nickel carbonyl[J]. Surf Sci, 2008, 602(3): 733-743. doi: 10.1016/j.susc.2007.12.008
-
[24]
曾波.核壳结构钴基催化剂及中间馏分油合成研究[D].太原:中国科学院大学山西煤炭化学研究所, 2014.ZENG Bo. Synthesis of middle distillates via cobalt-based catalysts with core-shell structures[D]. Taiyuan: Institute of Coal Chemistry, Chinese Academy of Sciences, 2014.
-
[25]
CHOU K, CHEN C. Fabrication and characterization of silver core and porous silica shell nanocomposite particles[J]. Microporous Mesoporous Mater, 2007, 98: 208-213. doi: 10.1016/j.micromeso.2006.09.006
-
[1]
-
表 1 NiO颗粒粒径及反应前后NiO@SiO2的核壳尺寸
Table 1. Particle size of NiO, core size and shell thickness of NiO@SiO2
Sample Core d/nm Shell d/nm NiO-350 4.9 - NiO-350@SiO2 5.1 6.1 Used NiO-350@SiO2 8.1 5.0 NiO-400 8.1 - NiO-400@SiO2 8.6 11.2 Used NiO-400@SiO2 10.6 10.1 NiO-500 23.7 - NiO-500@SiO2 23.3 23.0 Used NiO-500@SiO2 27.8 20.6 表 2 反应前后催化剂的表面原子浓度及体相Ni含量
Table 2. Surface atom concentration and Ni content of catalyst before and after reaction
Sample Surface atomic concentrationsa/% Ni/Si
(atomic ratio)Nib/% Ni Si O NiO-350@SiO2 10.11 17.77 72.12 0.57 57.32 Used NiO-350@SiO2 9.85 17.12 73.03 0.58 55.92 NiO-400@SiO2 8.50 24.36 67.14 0.35 58.98 Used NiO-400@SiO2 5.09 27.73 67.18 0.18 61.21 NiO-500@SiO2 6.46 21.22 72.32 0.30 60.68 Used NiO-500@SiO2 4.61 28.38 67.01 0.16 63.14 Theoretical valuec 33.50 11.00 55.50 3.05 62.16 a: the surface atomic concentrations of catalysts were calculated by XPS; b: Ni bulk concentration of catalysts obtained from ICP c: based on the addition mass when catalyst is prepared 表 3 反应前后催化剂的N2吸附
Table 3. N2 sorption of NiO@SiO2 before and after reaction
Sample BET surface area A/(m2·g-1) Pore volume v/(cm3·g-1) Pore diameter d/nm NiO-350@SiO2 117.2 0.218 7.4 Used NiO-350@SiO2 52.7 0.147 11.2 NiO-400@SiO2 82.9 0.197 8.2 Used NiO-400@SiO2 43.5 0.101 9.3 NiO-500@SiO2 34.4 0.074 8.6 Used NiO-500@SiO2 23.7 0.073 12.3 -

计量
- PDF下载量: 0
- 文章访问数: 1699
- HTML全文浏览量: 159