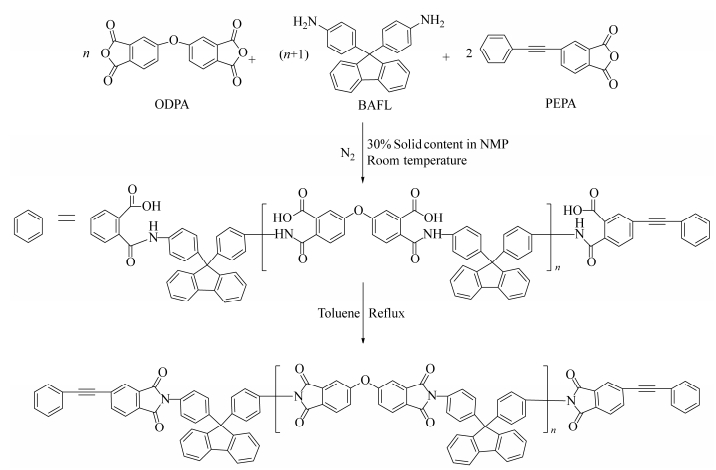

High Thermal Stable Polyimide Resins Derived from Phenylethynylendcapped Fluorenyl Oligoimides with Low Melt Viscosities
English
High Thermal Stable Polyimide Resins Derived from Phenylethynylendcapped Fluorenyl Oligoimides with Low Melt Viscosities
-
Key words:
- Polyimide
- / Fluorene
- / Proccessability
- / Thermal stability
- / Composite
-
INTRODUCTION
Owing to the great combination of high thermal stabilities and outstanding mechanical properties, aromatic polyimide resins have been considered as the desirable candidates as matrices of high temperature carbon fiber reinforced composites for the purpose of appropriate replacement of metallic components in aerospace and aviation applications[1-4]. However, it is difficult for hot-prees molding or autoclave process to yield complex and high-accuracy components. Hence, the resin transfer molding (RTM) technique has been universally studied for carbon fiber/polyimide (Cf/PI) composite fabrication, in which the requirement of polyimide resins appropriate for RTM process have become the key issue[5]. Furthermore, in order to meet the acquirement for higher flight speed and surface temperature of aircraft, higher heat-resisting level for Cf/PI composites was also needed. Therefore, seeking for the balance between melt-processable aromatic polyimides with both good thermal and mechanical properties has been a long-term existed scientific and technological challenge.
In the past few years, phenylethynyl-endcapped oligoimides (PEPA-oligoimides) have drawn great attention, especially with emphasis on the relationship between their chemical structures and melt viscosities, thermal and mechanical properties[6-9]. It is also noted that PEPA-oligoimides exhibited several advantages for RTM processing, including low and stable melt viscosity, no volatile evolution, and favorable chain extension over cross-linking reaction during thermal curing to produce thermoset resins with acceptable strength and toughness[5, 10-13]. However, there was still an obvious shortage for PEPA-oligoimides, for instance, the thermoset polyimide resin of phenylethynyl-terminated imide (PETI-5) produced lower glass transition temperature (Tg) (< 277℃) due to the incorporation of flexible segment in polymer backbone ensuring the appropriate melt fluidity[14].
In order to improve the thermal stability of the thermoset resin without sacrificing its melt processability, there has been a lot of reports focusing on improving Tg and decreasing the melt viscosities by reducing the MnCs of the resins, resulting in the development of PETI-298, PETI-330 and PETI-375[15, 16]. These PETI-series exhibited favorable melt stabilities of no more than 10 Pa·s at 280℃ for 2 h, their cured Tgs also increased gradually from 298℃ to 375℃. It was found that the low melt viscosity could be improved greatly by introducing bulky rigid substituents like 2, 3, 3', 4'-biphenyltetracarboxcylic anhydride (α-BPDA) into the backbone without deteriorating its thermal stability[17]. Recently, Ishida et al. have developed highly soluble polyimide resins by introducing 4, 4'-(9-fluorenylidene) dianiline (BAFL) groups into the backbones of TriA-PI which was prepared from α-BPDA, 4, 4'-diaminodiphenyl ether (4, 4'-ODA) and 4-phenylethynylphthalic anhydride (4-PEPA). The obtained thermoset resins have Tg in the range of 340-370℃, but their melt viscosities varied between 81-1810 Pa·s which did not meet the requirement for RTM process[18-21].
It is known that oligoimide derived from fluorene-containing monomer resulted in not only low melt viscosity but also high cured Tg due to its twisted bulky rigid structure. Besides, the PEPA end-capper provided high crosslink density of cured resin, beneficial for achieving high thermal stability. Furthermore, the dianhydride of 4, 4'-oxy-diphthalic anhydride (ODPA) aimed to increase the stiffness of polyimide backbone and reduce the melt viscosity of the oligoimide simultaneously ascribed to the presence of ether bond. In this study, for the purpose of obtaining resin matrix with high Tg and low melt viscosity, a series of PEPA-oligoimides with controlled molecular weights have been prepared by polycondensation of BAFL as fluorene-contained aromatic diamine, ODPA as flexible aromatic dianhydride and 4-PEPA as reactive end-capping reagent. Effects of the chemical structures on the melt processabilities of the oligoimides, the thermal and mechanical properties of the thermoset resins were systematically investigated. Moreover, primary evaluation of the polyimide resin as the matrix of carbon fiber reinforced composites was also performed.
EXPERIMENTAL
Materials
4-PEPA and ODPA were purchased from Changzhou Sunlight Fine Chemicals Co. Ltd (China) and Shanghai Institute of Synthetic Resin (China), respectively, dried under vacuum at 150℃ overnight prior to use. Commercially available N-methyl pyrrolidone (NMP) was obtained from Beijing POME Sci-tech Co. Ltd (China) and used without further purification. BAFL was synthesized in our laboratory according to the reported method[22]. Other reagents were commercially purchased from Sino Pharm Chemical Reagent Co. Ltd and Beijing Chemical Reagent Co. Ltd (China) and used as received. Plain woven carbon fiber cloth T300-3K was purchased from Jiangsu Tianniao High-tech Co. Ltd. (China).
Preparation of the PEPA-oligoimides with Designed MnCs
The PEPA-oligoimides with designed MnCs of 809-5000 g·mol-1 were prepared by reaction of BAFL with ODPA in the presence of 4-PEPA as a end-capping agent in NMP at elevated temperatures (Scheme 1). The molar ratio of PEPA:ODPA:BAFL was 2:n:(n+1), and the molecular weight was calculated by Eq. (1):
where Mn represents the calculated molecular weight of the oligoimide, MODPA, MODPA, MTFDB and MH2O represent the molecular weights of PEPA, ODPA, BAFL and H2O, respectively.
The preparation of the oligoimide resins can be illustrated by the following synthesis procedure. In a typical experiment, BAFL (9.10 g, 26 mmol) and NMP (10.00 g) were placed in a three-necked 100 mL flask, equipped with a mechanical stirrer, thermometer, dean stark trap, condenser and nitrogen gas inlet/outlet. The mixture was stirred at ambient temperature for a while until the aromatic diamine was completely dissolved. Subsequently, ODPA (1.90 g, 6 mmol) and 4-PEPA powders (10.00 g, 40 mmol) were added, residual 11.40 g of NMP was used to rinse all of the aromatic dianhydride into the flask, giving rise to a reaction mixture with 30% of solid content (W/W). The mixture was stirred overnight to form viscous poly(amic acid) resin solution. Next day, 3.50 g toluene was added into the solution which was heated and refluxed at 180℃ for 8 h. The water produced during thermal imidization was removed simultaneously by distillation with toluene cooled trap. After cooling down, the resin solution was poured into an excess of water-ethanol (V/V=1/1) to afford precipitation. After isolation by filtration, the oligomer powders were first dried at 100℃ overnight in air and subsequently dried at 202℃ under vacuum for another 4 h to yield yellow powders (19.0 g, yield 95%). Thus, OBP-PI-2 with MnC of 1000 g×mol-1 was obtained.
Similarly, other PEPA-oligoimides with MnC of 810 g×mol-1 (OBP-PI-1), 1500 g×mol-1 (OBP-PI-3), 2500 g×mol-1 (OBP-PI-4), 5000 g×mol-1 (OBP-PI-5), respectively, were prepared as shown in Table 1.
Code MnC (g·mol-1) ODPA (mol) BAFL (mol) PEPA (mol) OBP-PI-1 810 0.000 1.000 2 OBP-PI-2 1000 0.307 1.307 2 OBP-PI-3 1500 1.110 2.110 2 OBP-PI-4 2500 2.716 3.716 2 OBP-PI-5 5000 6.731 7.731 2 Table 1. Chemical compositions of the PEPA-oligoimides with designed MnCPreparation of the Thermal-cured Polyimide Neat Resins
The PEPA-oligoimide powders were placed into a die, which was then placed in a hot press preheated at 200℃. Then the die was heated to 350℃ at a rate of 4 K·min-1 and kept for 30-60 min, and during this period the die was gradually applied with a pressure of 2.0 MPa. Next the die was further heated to 370℃ and kept for another 2 h. After cooling below 100℃ with the applied pressure, the thermoset polyimide resin sheet was removed from the die and then cut into required sizes for the subsequent thermal and mechanical tests. The preparation procedure of the thermal-cured polyimide neat resins was shown as Fig. 1.
Characterization and Measurements
Nuclear magnetic resonance (1H-NMR) spectra were obtained on a Bruker AvanceⅢ400 spectrometer at frequencies of 400 MHz using DMSO-d6as solvents. The number-average molecular weights (Mn), the weight-average molecular weights (Mw) and the polydispersity index (Mw/Mn) were carried out by gel permeation chromatography (GPC) using a Waters 1515 high performance liquid chromatography (HPLC) pump, a Waters 2414 differential refractive index factor, and three Waters Styragel columns, using NMP as the eluent at a flow rate of 1.0 mL×min-1 at 35℃. The sample concentration was 1 mg×mL-1 and polystyrene was employed as the standard sample. Fourier transform infrared (FTIR) spectra were measured with pressed KBr pellets on a Tensor-27 Fourier transform spectrophotometer (Bruker, Germany).
Matrix-assisted laser desorption/ionization time of-flight (MALDI-TOF) mass spectra were carried out with a AutoflexⅢMALDI-TOF mass spectrometer (Bruker, Germany) equipped with delayed extraction, a multisample probe, a time-of-flight reflection analyzer, a nitrogen laser with a wavelength of 337 nm and a pulse width of 3 ns, and a linear flight path length of 100 cm, in which the flight tube was evacuated to 10-7 Pa. All measurements were performed in reflection mode and positive ion detection. The acceleration voltage was 19 kV and the delayed extraction voltage was 14.5-17 kV.
Wide-angle X-ray diffraction (WXRD) measurements were taken on a Rigaku D/max-2500 X-ray powder diffractometer with Cu/Kα radiation, operated at 40 kV and 200 mA. The 2θ scan data were collected in the scale of 5°-60°at a scan speed of 5 (°)×min-1.
Rheological behavior measurements were performed on AR2000 rheometer (TA Instruments, USA). Specimen disks (25.0 mm in diameter and 1.5 mm thick) were prepared by compression molding (10 atmospheres, 1 MPa) of the imide oligomer powders at room temperature. The disks were then loaded in the rheometer fixture with 25 mm diameter parallel plates. The top plate was oscillated at a fixed strain of 0.5% and a fixed angular frequency of 10 rad×s-1 while the lower plate was attached to a transducer, which recorded the resultant torque. For the tests of dynamic thermal melt complex viscosities, the test specimens were scanned at a heating rate of 4 K×min-1, in which the melt viscosity was determined.
Differential scanning calorimetry (DSC) measurements were conducted on a TA Q100 instrument in nitrogen atmosphere at a heating rate of 10 K×min-1. Thermo-gravimetric analyses (TGA) were performed on a TA Q50 instrument at a heating rate of 20 K×min-1 in nitrogen atmosphere at a flow rate of 60 cm3×min-1. Dynamic mechanical analyses (DMA) were performed on a TA Q800 analyzer with a heating rate of 5 K×min-1. A three-point bending mode was employed with the specimen size of 20 mm×5.0 mm×2 mm.
The dielectric constant values were tested using microwave dielectric permeability measurement system (E8363B, 40M-40GHz, Agilent-tech Co.Ltd) from 8-12 GHz using rectangular waveguide method at room temperature.
Mechanical properties of the thermo-setting PI neat resins and the Cf/PI composite laminates were measured on Instron 5567 universal testing machine (Instron, USA). Tensile strength and modulus tests for the neat resins were carried out in accordance with GB/T 16421-1996. Flexural strength and modulus measurements for the neat resins were obtained in accordance with HG/T 3840-2006. The interlaminar shear strengths of the Cf/PI composite laminates were measured on 6-ply quasi isotropic specimens, 20 mm×6 mm, at a span to depth ratio of 5 based on GB/T 1450.1-2005. The flexural strength and modulus tests for the composite laminates were obtained on specimens of 80 mm×12.5 mm, at a span to depth ratio of 32 based on GB/T 3356-1999. Five specimens were tested at 25, 250, 300 and 350℃, respectively.
The cross-sections of the composite laminates were observed through a field emission scanning electron microscope (S-4800, HITACHI, Japan), with the resolution ratio of 1.5 nm/15 kV.
Fabrication of Carbon Fiber/Polyimide (Cf/PI) Composite Laminates
The PEPA-oligoimide solution in dimethylacetamide (DMAc) with 30 wt% of solid content was impregnated into a plain woven carbon fiber cloth (desized by washing with acetone and then drying). The as-prepared carbon fiber prepregs were dried in an air circulating oven at 60℃/8 h and then cut into plies and piled up. The Cf/PI laminates were fabricated by thermal curing of the piled prepregs (6 ply) in a hot press in the following schedule: 80℃/0.5 h, 160℃/0.5 h, 200℃/0.5 h, 250℃/0.5 h and 360℃/1 h with a contact applied pressure, and then 360℃/1 h with an applied pressure of 2.5 MPa. Finally, the temperature rose to 370℃/2 h under the applied pressure to give thermally cured Cf/PI composite laminates. The composite laminates were cut into desired specimen sizes for testing of mechanical properties.
RESULTS AND DISCUSSION
Dielectric Properties of the Thermal-cured Polyimide Resins
Figure 12 depicts the dependence of dielectric constants of the thermoset polyimide resins on frequencies in the range of 8-12 GHz at ambient temperature. The dielectric constants were reduced from 3.15 to 2.83 while lowering the MnC from 5000 g×mol-1 to 810 g×mol-1. For instance, the OBP-PI-1 thermoset resin showed the lowest dielectric constant of 2.83, which did not obviously changed upon frequency in a broad range of 8-12 GHz. It was well known that the e of polymer materials could be deduced from the modified Clausius-Mossotti equation of
where P defined as the mole polarizability and V as the molecular free volume[30]. The low dielectric constant value can usually be achieved by introduction of substituents with low mole polarizability and big free volume. Similar results were also reported in the literature, such as the fluorene-containing PIs developed by Goto and his coworkers[31]. They have found that the introduction of fluorene moiety could decrease the ε value while keeping the high thermal stability, because it combined a short π-conjugation length with a bulky cardo aromatic structure. At the same time, the existence of bulky fluorenylidene moieties could reduce the imide fraction of repeating unit in polyimide, thus effectively lower the ε[31, 32].
Thermal Properties of the Thermal-cured Polyimides
Figure 9 compares the DSC curves of the uncured oligomer powders with different MnCs. It was obvious that no apparent melting endotherms were observed for the imide oligomers from OPI-PI-2 to OPI-PI-5. In comparison, OPI-PI-1 displayed a cusp melting endotherm which peaked at 321℃, but did not provide Tg, because it was just comprised of biphenylethynyl-endcapped BAFL, not really an imide oligomer[28]. Moreover, the exothermic grooves appeared above 370℃ of all oligomers were attributed to the complex reaction of the phenylethynyl groups, resulting in both chain extending and chain crosslinking, and the grooves moved to higher temperature as the MnC increased.
Figure 10 shows two representative TGA curves of the thermoset polyimide resins (OBP-PI-2 and OBP-PI-5) thermally cured at 370℃ for 2 h. All of the thermal-cured polyimides exhibited excellent thermal stabilities in N2 with the initial decomposition temperatures (Td) of more than 500℃ and the temperatures at 5% original weight loss (T5) in the range of 523-563℃(Table 5).
Code TGA DMA Tda (℃) T5b (℃) T10c (℃) Char (%) at 700℃ G'd (℃) G''e (℃) tanδf (℃) OBP-PI-1 557 563 585 75.4% 476 500 514 OBP-PI-2 551 557 578 74.0% 455 470 484 OBP-PI-3 531 537 565 71.6% 368 381 411 OBP-PI-4 515 523 557 71.0% 370 370 397 OBP-PI-5 550 553 581 70.4% 346 347 369 aTd: initial decomposition temperature; bT5: temperature at 5 wt% loss; cT10: temperature at 10 wt% loss; dG': onset temperature of the storage modulus curve; eG'': peak temperature of the loss modulus curve; f tanδ: peak temperature of the tand curve Table 5. Thermal properties of thermoset polyimide resinsFigure 11 compares DMA curves of the thermoset polyimide resins (OBP-PI-1and OBP-PI-5) with different MnCs. The storage modulus of the thermoset resin did not show obvious change until the temperature ramped up to the point (G') at which the storage modulus sharply droped down with the temperature going up. The G' ascended with decreasing the MnCs from 346℃ for OBP-PI-5 to 476℃ for OBP-PI-1. Moreover, The Tg values of the thermoset resins, defined as the peak of the tand value against temperature curve, increased from 369℃ for OBP-PI-5 to 514℃ for OBP-PI-1, respectively.
It is noteworthy that the BAFL-containing polyimides showed much higher Tg values than the corresponding BAFL-free polyimides with the similar molecular weights[27]. Actually, the high Tg of the thermoset polyimide resins are related to not only the cross-linking densities of polymer chains but also to the backbone rigidities, in which the cross-linking density was associated with the crosslinking reaction of phenylethynyl groups, and the backbone rigidity was linked with the rigid fluorene units. As the polymer became shorter, the crosslinking density increased, which resulted in higher Tg. Additionally, the presence of bulky pendent fluorene groups restricted the segment mobility, enhanced the rotational barrier of polymer chains and increased the time to complete glass process, which also led to a higher Tg. Because of the rigidity of the polymer chains, the subglass relaxation was hardly observed in the DMA tanδ curve[29].
Synthesis and Characterization of the PEPA-oligoimides with Designed MnC
The MnC of 809 g×mol-1 for OBP-PI-1 was designed to obtain a resin with polymerization degree of zero (DP=0), which was planned to obtain an oligoimide with the lowest melt viscosity. Then, the DP value gradually went up corresponding to the increase of MnC as 1000 g×mol-1 (OBP-PI-2), 1500 g×mol-1 (OBP-PI-3), 2500 g×mol-1 (OBP-PI-4) and 5000 g×mol-1 (OBP-PI-5), respectively. The oligoimides with the increased MnCs were thought to find the desirable balance among the melt viscosities of the oligoimides, the thermal stabilities and the mechanical properties of the thermoset resins.
It is deduced that the polyimide resins with high Tg and low melt viscosities could be accomplished by introducing of bulky and rigid cardo BAFL groups[23, 24]. Additionally, the incorporation of flexible linkage such as ether linkage in ODPA was also an effective pathway to reduce the melt viscosities and ascend the toughness of polymers.Moreover, the reactive phenylethynyl-endcapping groups in the oligomers would undergo favorable chain extension over cross-linking reaction during the thermal curing process to yield thermoset resins with acceptable strengths and toughness even if the oligomers had lower MnC. Hence, the combination of ODPA, BAFL and PEPA was expected to produce PEPA-oligoimides with low melt viscosities and corresponding thermal cured polyimide resins with high Tg.
The chemical structures of the PEPA-oligoimides were characterized by following various methods. Figure 2 is a typical 1H-NMR spectrum of the PEPA-oligoimide (OBP-PI-2) in dimethyl sulfoxide-d6 (DMSO-d6), in which all of the protons in the chemical structure of OBP-PI-2 have been assigned as expected, implying that the oligoimides obtained have the prospective chemical structures. It is shown that the amino group (―NH2) in BAFL at the chemical shift of δ=4.91 disappeared and no proton peak of carboxylic acid (―COOH) appeared over δ=10, demonstrating that the monomers have totally transformed into the designed oligoimide structure.
The molecular weights of the PEPA-oligoimides were measured by GPC as shown in Fig. 3 and the data of Mn, Mw and Mw/Mn are summarized in Table 2. It is noteworthy that the Mns of the oligoimides were 1.4-3.2 times higher than the calculated ones. For instance, the Mn of OBP-PI-3 determined by GPC was 4000 g×mol-1, about 2.7 times of the MnC (1500 g×mol-1). The polydispersities (Mw/Mn) were measured in the range of 1.02-1.63. The retaining time before the major molecular weight peaks appeared was shortened as the MnC increased. For example, OBP-PI-1 with the lowest MnC showed an elution peak at 19.4 min, compared to 17.1 min of OBP-PI-3 and 15.8 min of OBP-PI-5, respectively. Other literatures also reported the similar results that the Mn determined by GPC were greater than the calculated Mn[25]. Actually, the GPC results showed the same trend with the designed molecular weights values, implying that the molecular weights of the PEPA-oligoimides could be controlled by precisely adjusting the MnC.
Code MnC (g·mol-1) Mn (g·mol-1) Mw (g·mol-1) Mw/Mn OBP-PI-1 810 1800 1800 1.00 OBP-PI-2 1000 3200 3900 1.22 OBP-PI-3 1500 4000 5300 1.33 OBP-PI-4 2500 4400 6400 1.45 OBP-PI-5 5000 7100 11600 1.63 Table 2. GPC data of the PEPA-oligoimides with different molecular weightsFigure 4 compares the FTIR spectra of the PEPA-oligoimides with different MnCs. The asymmetric and symmetric stretching absorption bands around 1780 and 1720 cm-1, as well as the bending vibration absorption band around 725 cm-1 were attributed to the imide groups (C=O) in the oligoimide backbone; Meanwhile, the absorption at 1380 cm-1 assigned to the vibration of the C―N in the imide five-membered ring was also detected; Additionally, the absorption at 2210 cm-1 was attributed to the stretching vibrations of ethynyl groups (―C≡C―) in the oligomer. The absorption at 2210 cm-1 became weakened in intensity as the MnC increased, implying the content of PEPA gradually diminished. Evidently, the oligoimides with phenylethynyl endcapping groups have been definitely acquired.
Figure 5 compares the MALDI-TOF mass spectra of the PEPA-oligoimides with different MnCs and Table 3 summarizes the molecular structures of the oligoimide species detected. It can be inferred that the oligoimides were oligomer mixtures with different molecular weights. For instance, OBP-PI-1 had only one peak located at m/z=831.9, giving a molecular weight of 808.9 (831.9-23=808.9) corresponding to the PEPA-oligoimide with DP=0, which was well in accordance with the MnC. In comparison, OBP-PI-4 contains three oligomer species with molecular weights of 1431.5 (1454.5-23.0, DP=1, relative intensity=0.92), 2054.2 (2077.2-23.0, DP=2, relative intensity=1.00), and 2654.0 (2677.0-23.0, DP=3, relative intensity=0.27), respectively. In addition, OBP-PI-5 showed much more complex mass spectra, as many as six oligomer species with molecular weights from 1431.5 (DP=1) to 4544.9 (DP=6) were all detected. It could be deduced that the oligoimides had wider molecular weight distribution and higher molecular weight chemical species as the MnC increased. Clearly, the real molecular weights of the prepared PEPA-oligoimides are not the same as expected, however, it was still a valid pathway to control the molecular weights of the oligoimides by adjusting the MnC.
No. Chemical structures of the PEPA-oligoimide species m/z 0 831.9 1 1454.5 2 2077.2 3 2677.0 4 3322.5 5 3945.2 6 4567.9 Table 3. Chemical structures of the PEPA-oligoimides detected by MALDI-TOFFigure 6 depicts X-ray diffraction patterns of the oligoimides with different MnCs. When the oligoimide with the MnC of 900 g×mol-1 was added, it was obvious that as the MnC increased, the morphology of the PEPA-oligoimides varied from somewhat crystalline phase to amorphous phase. This result implied that the increased concentration of ODPA in the polyimide backbone might reduce the crystallinity of the PEPA-oligoimide, probably due to the fact that the ether linkage of ODPA increased the flexibility of chain and reduced the interaction between chains[26].
Mechanical Properties of the Thermoset Polyimide Neat Resins
Table 6 summarizes the mechanical properties of the thermoset polyimide neat resins at room temperature. The thermoset polyimide resins thermally cured at 370℃/2 h showed mechanical properties with tensile strengths in the range of 13.6-65.4 MPa, tensile moduli of 1.4-2.2 GPa and elongations at breakage of 1.3%-2.8%. As the MnC of oligoimide increased, the tensile strength of the thermoset polyimide resin was improved from 13.6 MPa for OBP-PI-1 to 65.4 MPa for OBP-PI-5, and the flexural strength increased from 13.4 MPa for OBP-PI-1 to 108.7 MPa for OBP-PI-5. Additionally, the elongation at breakage of the thermoset resin was also improved from 1.3% for OBP-PI-1 to 2.8% for OBP-PI-5. There was a position correlation between the mechanical strengths and the MnC (Fig. 13), the higher the MnC was, the better the mechanical properties could be. Unlike the short molecular chain, the longer chain was more flexible and easy to change shape. When under given stress, it was likely to form a compact structure which could avoid defects and give better mechanical properties.
Code Tensile properties Flexural properties Strength (MPa) Modulus (GPa) Elongation (%) Strength (MPa) Modulus (GPa) OBP-PI-1 13.6 - 1.3 13.4 1.8 OBP-PI-2 27.8 1.4 1.8 49.6 3.0 OBP-PI-3 34.3 1.6 2.0 57.2 3.2 OBP-PI-4 42.7 1.8 2.8 61.1 3.4 OBP-PI-5 65.4 2.2 2.8 108.7 3.6 OBP-PI-1 13.6 - 1.3 13.4 1.8 Table 6. Mechanical properties of the thermoset polyimide resinsThermal and Mechanical Properties of Cf/PI Composite Laminates
Based on the melt processabilities of the oligoimides and the mechanical and thermal properties of the thermoset neat resins, OBP-PI-3 with MnCof 1500 g×mol-1 was selected as the matrix to prepare Cf/PI composite laminates by hot-press molding, which had the minimum melt viscosity of 4.2 Pa·s at 311℃ and the thermoset neat resin which thermally cured at 370℃ for 2 h has Tg of 411℃(tand peak value) by DMA, tensile and flexural strength of 34.3 and 57.2 MPa, respectively.
T300 carbon fiber cloth prepreg was prepared by impregnating carbon fiber plain woven cloth with the DMAc solution of OBP-PI-3 oligoimide. The prepreg was cut into desired size in accordance with mechanical test requirements and plied up, and then thermally cured at 370℃ in hot press with applied pressure of 2.5 MPa. SEM result indicated that the thermoset polyimide resin combined very well with carbon fiber cloth and no defects or voids were observed in the interface (Fig. 14). The Tg of the Cf/PI composites was measured at 410℃(tanδ peak value) by DMA after post-cured at 380℃ for 4 h, which was almost the same as that of the thermoset neat resin.
Table 7 shows the mechanical properties of the T300/OBP-PI-3 quasi isotropic composite laminates tested at elevated temperatures. The flexural strengths of the composite were 479 MPa at 25℃, 355 MPa at 250℃(retention rate, r.r.=74.1%), and 254 MPa at 350℃(r.r.=53.0%), respectively. The flexural modulus was 30 GPa at 25℃ and 25 GPa at 350℃(r.r.=83.3%), respectively, showing great strength and modulus retention at high temperature. The interlaminar shear strength (ILL) was 32 MPa at 25℃, 27 MPa at 300℃(r.r.=84.4%) and 20 MPa at 350℃(r.r.=62.5%), respectively. Although the initial ILL value of Cf/PI composite laminates was lower than that of normal Cf/PI composites, the ILL retention rate at 350℃ was measured as high as 62.5%, implying that this Cf/PI composites had great thermal stability, probably being long-term served at temperature of as high as 350℃.
Mechanical properties Temp. (℃) Tested results Flexural strength (MPa) 25 479 r.r.% a 250 355 74.1 300 303 63.2 350 254 53.0 Flexural modulus (GPa) 25 30 - 250 28 93.3 300 26 86.7 350 25 83.3 Interlayer shear strength (MPa) 25 32 - 250 30 93.7 300 27 84.4 350 20 62.5 Table 7. Mechanical properties of Cf/PI composite (T300/OBP-PI-3) at elevated temperaturesMelt Processabilities of the PEPA-oligoimides
Figure 7 displays the complex melt viscosities of the representative oligoimides (OBP-PI-1, OBP-PI-2 and OBP-PI-4) with different MnCs against temperature. The melt viscosity curves first descended significantly, reached to the lowest points and then ascended with ramping up temperature from 200℃ to 380℃ at a heating rate of 4 K×min-1, implying that the oligoimides yielded melt fluid with low viscosities at first, and then thermally cured to give partly cured polyimide resins with the increased melt viscosities. Table 4 summarizes the melt viscosities of the oligoimides with different MnCs at three different temperatures. The minimum melt viscosity of the oligoimide went down gradually with decreasing the MnC. For instance, the minimum melt viscosity of OBP-PI-4 was 340 Pa·s at 353℃, which decreased to 4.2 Pa·s at 311℃ for OBP-PI-3, 1.2 Pa·s at 324℃ for OBP-PI-2 and 0.2 Pa·s at 312℃ for OBP-PI-1, respectively. Evidently, the lower the MnC value was, the weaker the intermolecular force was, and the better the chain moving ability could be. Meanwhile, the melt processing window, i.e. the temperature width wherein the resin was in the lower viscosity stage suitable for melt processing, became wider as the MnC decreased. It was obvious that the oligoimide with shorter chain length owned more contents of PEPA-endcapped groups than the longer one, thus, it should have taken more time to complete the crosslinking reaction. This might be the reason why the oligoimide with a lower molecular weight had more time with a lower viscosity. Besides, the mass center of molecules with low Mn value could be easily transferred when the specimen was heated. However, the movement of the molecule with larger Mn was harder. In the preparation of the multilayer composite, the resin with low melt viscosity tended to yield a high-quality product with little void. In addtion, the presence of pendent bulky fluorene components lengthening the interchain distance, enlarging the free volume and weakening the interaction of the polymer backbone, also resulted in relatively low melt viscosity of the oligoimide.
Table 4. Melt viscosities of the PEPA-oligoimides with different MnCs at different elevate temperatures
Code Complex viscosity (Pa·s) Minimum melt viscosity (Pa·s) Melt viscosity changes for 1 h (Pa·s) 280℃ 320℃ 360℃ OBP-PI-1 0.4 0.2 89.5 0.2 Pa·s at 312℃ 0.35-220 (270℃) OBP-PI-2 7.5 1.3 57.9 1.2 Pa·s at 324℃ 0.97-227 (270℃) OBP-PI-3 5.7 4.6 187.5 4.2 Pa·s at 311℃ 25.3-7456 (290℃) OBP-PI-4 38320 913 392 340 Pa·s at 353℃ 960-83640 (340℃) OBP-PI-5 14650 30150 34580 2936 Pa·s at 336℃ - Table 4. Melt viscosities of the PEPA-oligoimides with different MnCs at different elevate temperaturesThe melt stabilities of the PEPA-oligoimides were also evaluated by heating the test specimens at a heating rate of 4 K×min-1 from 100℃ to the desired temperature and subsequently stayed at the temperature for 1 h. Figure 8 compares the melt viscosity stability curves of oligoimides which were firstly heated up and then kept at a certain temperature (270℃ for OBP-PI-1, 270℃ for OBP-PI-2, 290℃ for OBP-PI-3, 340℃ for OBP-PI-4, respectively) for 1 h. The reason why we compared their melt viscosity stabilities at different isothermal temperatures was that as the MnC increased, the temperature in which the PEPA-oligoimide reached to the minimum viscosity delayed to a higher value, and generally the isothermal temperature was set before the PEPA end-capper began to crosslink drastically at 350℃[27]. It can be seen that at the temperature ramping step, a sharp drop in melt viscosity was observed due to the melting of the oligoimide, then the melt viscosity increased slowly at the isothermal stage owing to the chain-extending and cross-linking reactions of the phenylethynyl groups at elevated temperatures. For instance, the melt viscosity of OBP-PI-2 was 0.97 Pa·s at 270℃, increased gradually to 227 Pa·s after isothermal standing for 60 min at 270℃, implying good melt stability.
Hence, the PEPA-oligoimides with lower MnCs from OBP-PI-1 to OBP-PI-3 showed the minimum melt viscosities in the range of 0.2-4.2 Pa·s at 310-325℃, which were suitable for RTM processing of Cf/PI composites to produce complex and high-precision large component, another oligoimide OBP-PI-4 with melt viscosity of 340 Pa·s at 353℃ was appropriate for autoclave processing or hot-prees molding.
CONCLUSIONS
In this work, a series of phenylethynyl-endcapped fluorenyl cardo oligoimides were prepared. Experiment results indicated that the introduction of bulky fluorene groups enlarged the free volume among the molecular chains, which caused low melt viscosity and improved the melt processability of the oligoimides. At the same time, due to the thermal stability of the fluorene-containing molecular chain, these polyimide obtained high cured Tg. Lower molecular weight tended to reduce the melt viscosity, and higher molecular weight was beneficial for the mechanical properties. OBP-PI-3 with MnC of 1500 g×mol-1 was selected as the matrix resin to fabricate the Cf/PI composite laminates, which showed excellent mechanical strength retention (r.r.%) at temperature of as high as 350℃, including r.r.% of 53.0% for flexural strength, 83.3% for flexural modulus and 62.5% for interlayer shear strength, respectively, might be long-term served at high temperature in aerospace and aviation industry.
-
-
[1]
Serafini, T.T., Delvigs, P. and Lightsey, G.R., J. Appl. Polym. Sci., 1972, 16:905 doi: 10.1002/app.1972.070160409
-
[2]
Wilson, D., Brit. Polym. J., 1988, 20:405 doi: 10.1002/(ISSN)1934-256X
-
[3]
Jensen, B. and Chang, A., High Perform. Polym., 1998, 10:175 doi: 10.1088/0954-0083/10/2/002
-
[4]
Hergenrother, P.M., High Perform. Polym., 2003, 15:3
-
[5]
Smith, J., Connell, J.W., Hergenrother, P. and Criss, J., J. Compos. Mater., 2002, 36:2255 doi: 10.1177/0021998302036019293
-
[6]
Hergenrother, P.M., Connell, J.W. and Smith, J., Polymer, 2000, 41:5073 doi: 10.1016/S0032-3861(99)00569-8
-
[7]
Yu, P., Wang, Y., Yu, J.R., Zhu, J. and Hu, Z.M., Chinese J. Polym. Sci., 2016, 34(1):122 doi: 10.1007/s10118-016-1733-4
-
[8]
Yang, M., Wang, D.M., Sun, N.W., Chen, C.H. and Zhao, X.G., High Perform. Polym., 2015, 27:449 doi: 10.1177/0954008314555521
-
[9]
Sun, L., Wang, W., Xu, L.B., Chen, G.F. and Fang, X.Z., High Perform. Polym., 2015, DOI: 10.1177/0954008315610394
-
[10]
Rao, X., Zhou, H., Dang, G., Chen, C. and Wu, Z., Polymer, 2006, 47:6091 doi: 10.1016/j.polymer.2006.06.037
-
[11]
Yokota, R., Yamamoto, S., Yano, S., Sawaguchi, T., Hasegawa, M., Yamaguchi, H., Ozawa, H. and Sato, R., High Perform. Polym., 2001, 13:S61
-
[12]
Connell, J.W., Smith Jr, J.G. and Hergenrother, P., J. Macromol. Sci. Polym. R., 2000, 40:207 doi: 10.1081/MC-100100585
-
[13]
Wang, D.H., Baek, J.B., Nishino, S.F., Spain, J.C. and Tan, L.S., Polymer, 2006, 47:1197 doi: 10.1016/j.polymer.2005.12.061
-
[14]
Smith Jr, J., Connell, J. and Hergenrother, P., J. Compos. Mater., 2000, 34:614 doi: 10.1177/002199830003400705
-
[15]
Bryant, R.G., Jensen, B.J. and Hergenrother, P.M., J. Appl. Polym. Sci., 1996, 59:1249 doi: 10.1002/(ISSN)1097-4628
-
[16]
Hergenrother, P. and Smith, J., Polymer, 1994, 35:4857 doi: 10.1016/0032-3861(94)90744-7
-
[17]
Chern, Y.T., Tsai, J.Y. and Wang, J.J., J. Polym. Sci., Part A:Polym. Chem., 2009, 47:2443 doi: 10.1002/pola.v47:9
-
[18]
Ogasawara, T., Ishikawa, T., Yokota, R., Ozawa, H., Taguchi, M., Sato, R.; Shigenari, Y. and Miyagawa, K., Adv. Compos. Mater., 2002, 11:277 doi: 10.1163/156855102762506317
-
[19]
Ogasawara, T., Ishida, Y., Yokota, R., Watanabe, T., Aoi, T. and Goto, J., Compos. Part A-Appl. S., 2007, 38:1296 doi: 10.1016/j.compositesa.2006.11.007
-
[20]
Sasaki, T. and Yokota, R., High Perform. Polym., 2006, 18:199 doi: 10.1177/0954008306058269
-
[21]
Ishida, Y., Ogasawara, T. and Yokota, R., High Perform. Polym., 2006, 18:727 doi: 10.1177/0954008306068250
-
[22]
Qian, Y. and Huang, W., 2010, U.S. Pat., 5, 387, 725
-
[23]
Kuroki, T., Shibuya, A., Toriida, M. and Tamai, S., J. Polym. Sci., Part A:Polym. Chem., 2004, 42:2395 doi: 10.1002/(ISSN)1099-0518
-
[24]
Zuo, H., Chen, J., Hu, A., Fan, L. and Yang, S., Eur. Polym. J., 2007, 43:3892 doi: 10.1016/j.eurpolymj.2007.06.009
-
[25]
Miyauchi, M., Ishida, Y., Ogasawara, T. and Yolota, R., Polym. J., 2013, 45:594 doi: 10.1038/pj.2012.160
-
[26]
Zhang, C.H., Su, G.D., Chen, H., Sun, Y., Song, H.R. and Tong, L.L., J. Appl. Polym. Sci., 2015, 132:41303
-
[27]
Cho, D. and Drzal, L.T., J. Appl. Polym. Sci., 2000, 76:190 doi: 10.1002/(ISSN)1097-4628
-
[28]
Su, C. n., Ji, M., Fan, L. and Yang, S.Y., High Perform. Polym., 2011, 23:352 doi: 10.1177/0954008311410997
-
[29]
Coburn, J.C., Soper, P.D. and Auman, B.C., Macromolecules, 1995, 28:3253 doi: 10.1021/ma00113a030
-
[30]
Zhao, X.J., Liu, J.G., Rui, J.M., Fan, L. and Yang, S.Y., J. Appl. Polym. Sci., 2007, 103:1442 doi: 10.1002/(ISSN)1097-4628
-
[31]
Goyo, K., Kakuta, M., Inoue, Y. and Matsubara, M., J. Photopolym. Sci. Tec., 2000, 13:313 doi: 10.2494/photopolymer.13.313
-
[32]
Goyo, K., Inoue, Y. and Matsubara, M., J. Photopolym. Sci. Tec., 2001, 14:33 doi: 10.2494/photopolymer.14.33
-
[1]
-

计量
- PDF下载量: 0
- 文章访问数: 753
- HTML全文浏览量: 2