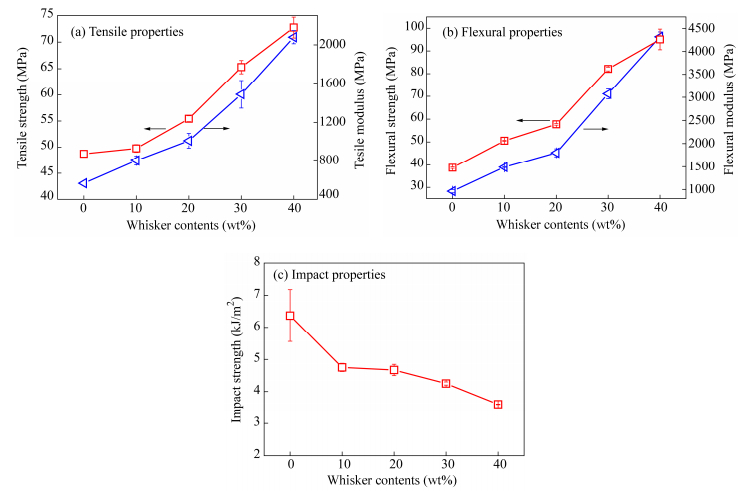

High Performance Long Chain Polyamide/Calcium Silicate Whisker Nanocomposites and the Effective Reinforcement Mechanism
English
High Performance Long Chain Polyamide/Calcium Silicate Whisker Nanocomposites and the Effective Reinforcement Mechanism
-
Key words:
- PA1012
- / Calcium silicate whisker
- / No coupling agent
- / Homogeneous dispersion
- / Enhanced properties
-
INTRODUCTION
Long chain polyamide (LCPA), with excellent properties, has been emerged as an important engineering plastics in various fields. Having more than ten methylene groups in recurring amide group, LCPA owns lower water absorption and improved toughness compared with common polyamide like PA66 whose mechanical properties are extremely sensitive to humidity and could be tremendously destroyed by absorbed water[1, 2]. However, due to relatively lower hydrogen bonding density, the mechanical strength of LCPA is imperative to be developed especially in some highly demanded applications, where properties like thermal stability and high strength are priorities[3-7].
The incorporation of filler, such as clay, whisker, carbon black and fiber, into polyamide is a simple and effective method for upgrading properties[8-14]. Whisker, among the most promising candidates, is a kind of commonly used reinforcements whose strength approaches maximum theoretical value owing to its limited internal defects. In this way, remarkable increase of mechanical properties of polymer can be expected. Potassium titanate[15-17], silicon nitride[18, 19], alumina[20, 21], silicon carbide[22] and cellulose[12, 23] are among the extensively used whiskers in the research of reinforced polyamide. Tjong et al. prepared PA6/potassium titanate composites by melt blending in which filler surface was modified with tetrabutyl orthotitanate prior to mixing[16, 24]. Yang et al. reported that the notched impact strength enhanced 64% after addition of silicon nitride whiskers into PA6 matrix[18]. Three kinds of alumina whiskers including purified fibers, ribbon-shaped fibers and silica-coated fibers were melt mixed with PA12 and the corresponding rheology, morphology and thermal behaviors were investigated[20].
It is well established that the key factors, determining final properties of polymer composites, are dispersion quality and interfacial adhesion of two phases[3, 25-27]. Unfortunately, fillers usually exhibit poor interaction with polymer leading to agglomeration in matrix and desired performance couldn’t be obtained. A striking character was found from previous researches, in order to develop loadbearing capacity, most whiskers were modified with coupling agents such as maleate and alkyl silanes which could establish better interaction with both the matrix and filler, or employing elaborated approaches such as in situ polymerization and emulsion polymerization through which a better dispersion of whisker could be reached[28, 29]. For example, to further enhance dispersion quality and interfacial adhesion of potassium titanate whiskers in PA6, Chen et al. adopted in situ polymerization method in which whiskers were also modified with an alkylsilane coupling agent[15]. Miniemusion polymerization, used a stable aqueous dispersion including cellulose whiskers and a poly(styrene-co-hexylacrylate), was adopted to fabricate nanocomposites, in which reactive silane was added to avoid particle agglomeration[28]. Both composites prepared above exhibited improved mechanical properties and thermal stability. However, both complicated processing and high production cost of dispersed phase tremendously limit its application in large scale. Furthermore, when second phase was added into polymer matrix, another significant aspect should be taken into account is that the crystallization of host polymer may be remarkably disturbed during processing, which may significantly affect physical properties[20, 30]. Therefore, much attention should be paid to those inorganic fillers with low cost and strong interaction with host polymer.
In our research, calcium silicate whisker, produced by calcium oxide and desilicated solution of fly ash through hydrothermal reaction, was attempted to be introduced into long chain polyamide, in which the fly ash was one of the residues generated in combustion. This whisker is a promising reinforcement of thermoplastics, which has distinct advantages of low cost and superior physical properties. Polyamide 1012 (PA1012)/calcium silicate whisker nanocomposites were prepared by simple twin screw extruder, in which the content of whisker ranges from 10 wt% to 40 wt%. Without chemical surface modification or coupling agent coating, the effect of whisker on the LCPA matrix was investigated from aspects of the morphology, the mechanical properties and thermal properties. Thus corresponding mechanism of improved properties was put forward considering the interaction of two components. Optimal content range of filler in polyamide was determined by varying contents of calcium silicate whisker. At last, water absorption, a significant factor of influencing mechanical properties of polyamide, was discussed for neat polyamide as well as nanocomposites.
Experimental
Mechanical Measurement
The tensile properties of the nanocomposites were detected using an Instron device (Instron 3365) at 23 ℃ with the crosshead speed of 50 mm/min. The three-point flexural tests were also carried out in this instrument with the crosshead speed of 5 mm/min and a span of 64 mm.
The Izod impact strength measurements were carried out with impact tester (XJC-25D) using a 1 J hammer. Samples with notched were employed and all mechanical measurements were repeated 5 times in which average values were used for analysis.
Morphological Analysis
The as-received calcium silicate whisker, the fractured surfaces of samples after impact tests and the longitudinal cross section of injection molded sample were coated with a layer of gold and the morphology was examined by the scanning electron microscopy (SEM, JSM-6700F).
Materials and Sample Preparation
PA1012 (―[HN(CH2)10NHCO(CH2)10CO]n―, melting temperature=189 ℃, melt flow rate (MFR)=1.39 g/10min (190 ℃/2.16 kg)), supplied by Shandong Guangyin New Materials Co., Ltd., is synthesized with decamethylene diamine and dodecanedioic acid in which the acid monomer is bio-fermenting source. Calcium silicate whiskers (an aspect ratio of 10-100), representing fluffy needle-like shape, are produced by Institute of Process Engineering, Chinese Academy of Sciences. Both materials are dried under vacuum at 100 ℃ for 12 h prior to use.
Composites of PA1012/calcium silicate whisker with the weight ratio of 100/0, 90/10, 80/20, 70/30, 60/40 were melt mixed in a twin-screw extruder at 210 ℃ for 7 min. In mixing process, to avoid weight loss of whiskers, part of PA1012 pellets were introduced into mixer, followed by calcium silicate whiskers and the rest of pellets were added at last. The obtained blends were injection molded into standard bars which were put in ambient for 24 h before mechanical measurements. In this article, the weight ratio of whiskers was used to express nanocomposite components PAC-x (PAC denotes the PA1012/calcium silicate whisker nanocomposites, x means the weight fraction of calcium silicate whisker in the nanocomposites. For example, PAC-10 denotes 10 wt% whiskers with respect to the total weight of the composite).
Thermal Properties
Thermal behaviors of PA1012/calcium silicate whisker nanocomposites were measured by differential scanning calorimeter (TA Q2000) which was calibrated in indium standard. Each specimen of about 5 mg sealed in an aluminum pan was tested under N2 atmosphere at a constant flow rate. The first cooling and the second heating runs were recorded in all the measurements.
Thermal gravimetric analysis (TGA, PE Pyris 1) was utilized to determine the onset temperature of degradation. The sample of 2 mg was tested with a heating rate of 10 K/min from 50 ℃ to 750 ℃.
Vicat Softening Temperature
The Vicat softening temperature was determined using a Vicat softening temperature tester (Chengde Jinjian Testing Instrument CO., LTD, HDT/V-3116). The surface of sample with the dimension of 1 cm × 1 cm × 0.5 cm was rested by a penetrating needle and a load of 50 N was applied on the specimen. An oil bath was employed to heat the specimens at a rate of 120 K/h.
Water Absorption Measurement
Water absorption measurements were carried out using the injection bar which was prepared for mechanical test and dried at 80 ℃ in vacuum to reach a constant weight prior to immersion into water. The dried bars were completely put into boiling water for 1-7 h, which were removed and dried with filter paper, and mass measurement was taken at one hour interval. The percent of water absorption was calculated by the Eq. (1). In this paper, the samples after water absorption were marked as PA1012-w.
where the dry weight is the initial weight after dry and wet weight is the weight after immersion period. Four specimens were tested in this test for each sample and the average value was used to evaluate total water absorption.
RESULTS AND DISCUSSION
Mechanical Properties of PA1012/Calcium Silicate Whisker
The variations of mechanical strength and modulus versus whisker contents are indicated in Fig. 4, which includes tensile properties, flexural properties and impact properties. From Figs. 4(a) and 4(b), it is noticed that the tensile strength, flexural strength and corresponding modulus increase remarkably with whisker contents. Compared with neat PA1012, a 34% and 164% increase in tensile strength and Young’s modulus is observed in PA1012/calcium silicate whisker nanocomposites with 30 wt% whisker content. The contribution is more pronounced for flexural properties that the flexural strength and modulus is raised by 112% and 219% respectively. However, a slight reduction of elongation at break in tensile test as well as the Izod notched impact strength is accompanied after incorporation of calcium silicate whisker, which is a common case in nanocomposite system ascribed to debonding of fillers from matrix. As revealed in Fig. 1, a small portion of whiskers are detached from the matrix, but most can bond well. The impact strength of PAC-20 is 4.75 kJ/m2 as opposed to that of 6.37 kJ/m2 of neat polyamide, indicating the decrease of ductility, but it limits in an accepted level. By evaluating both the mechanical strength and toughness, the critical content of whiskers is around 20 wt%. That is to say, the range of whisker content less than 20 wt% is preferred, beyond which an increase of rigidity comes. The above analysis ascertains the excellent reinforcement effect of calcium silicate whisker on LCPA.
Figure 4. Mechanical properties of injection molded PA1012/calcium silicate whisker nanocomposites for (a) tensile properties, (b) flexural properties and (c) impact properties
Based on the mechanical data, the mechanism of calcium silicate whisker reinforced PA1012, illustrated in Scheme 1. Calcium silicate whisker used in the research is produced by calcium oxide and desilicated solution of fly ash. Through this, large amounts of hydroxyl groups are definitely generated in the surface of the calcium silicate whiskers. The chemical structure of PA1012 (HN(CH2)10NHCO(CH2)10CO) exhibits recurring carboxyl group in the repeating unit. Thus it is possibly that the hydroxyl group in the whisker surface is attracted by carbonyl group in polyamide chain and hydrogen bonding is established at the interface of matrix and whiskers. This results in compatibility of two phases and is one of the most important factors in determining physical properties. Additionally, with needle-like shape, calcium silicate whisker is favorable to intercalate in matrix so that it can be distributed evenly in the matrix[20, 33]. Both uniform dispersion and strong interaction of two phases endow it a higher efficiency of load transfer. During molded injection process, calcium silicate whisker is oriented well in the flowing direction, as represented in Fig. 3, which further improves the final properties. It is interesting to find that the tensile strength of PA1012 is larger than flexural strength, which is opposite to other semi-crystalline polymers. This phenomenon arises from the great contribution of strain-induced crystallization to the stress enhancement at large strain. From the statement above, it can be concluded that the incorporation of calcium silicate whisker without a coupling agent enables to significantly enhance tensile and flexural properties while the decrease of impact strength is weak, which confirms the existence of excellent stress-transfer properties in PA1012/calcium silicate whisker. In this aspect, the calcium silicate whisker is extremely suitable for reinforcement of PA1012.
Morphology
The morphology of as-received calcium silicate whisker is shown in Fig. 1, in which whiskers are oriented randomly and exhibit an aspect ratio of 10-100 with fluffy needle-like shape. It should be pointed out that the whisker morphology in SEM images appears much brighter, certainly owing to charging during taking a photo. Figure 2 reveals SEM observations of specimens after impact tests taken from transverse directions, suggesting filler distribution. Apparently, whiskers are distributed homogeneously in PA1012 matrix even with the high whisker concentration of 40 wt% and agglomeration, resulting from ultrafine structure, is not observed. In general, without coupling agent, realization of uniform dispersion is a big challenge by traditional twin-screw extruder[31, 32]. Consequently, it is a highlight in our research that, even with large filler content, better dispersion of calcium silicate whisker in LCPA can be realized without chemical treatment. Moreover, the adhesion of two components shows a strong connection between matrix and whisker. These are key points to make whiskers bear stress synchronously and evenly so that a satisfactory reinforcing efficiency can be approached[24]. The longitudinal distribution of calcium silicate whisker in injection molded composite is represented in Fig. 3 implying a well oriented microstructure of filler. Most of whiskers are oriented along shear flow direction in injection molded field and this definitely facilitates the enhancement of physical performance. Here the superior dispersion of calcium silicate whisker is attributed to its large surface area and intense interaction with polyamide matrix and the concrete reasons will be interpreted in latter section.
Melting and Crystallization Behavior
As aforementioned, the crystallization behavior may be altered after incorporation of fillers, which is detrimental to matrix mechanical performance[1, 2]. DSC tests are performed in our research and the results are recorded in Fig. 6, in which the heat of fusion has been corrected by weight fraction of PA1012. For crystallization peaks, the peak of neat PA1012 located at around 163.6 ℃ is observed while the peaks of nanocomposites shift to higher temperature indicating that whiskers act as nucleating agents. However, the melting temperature, which is closely related to the thickness of the crystals, keeps constant showing that the lamellae thickness almost has no change after incorporation of whisker in polyamide. Additionally, the heat of flow (ΔHc) of neat polyamide and nanocomposites, which has been corrected by weight fraction of PA1012 in the nanocomposites, is summarized in Table 2 and shows increase of ΔHc after addition of calcium silicate whisker. This strongly verifies the development of the degree of crystallinity and it should be a part of contribution to improved performance involving mechanical properties and water barrier properties. It is interesting to find that the value of ΔHc in nanocompsite, although larger than that of pure polyamide, has a decrease trend beyond the content of 20 wt%, which is consistent with our results in mechanical properties part that the optimal whisker content is around 20 wt%. Excessive filler destroys the original crystallization instead of working as a nucleating agent. Similar rules are also observed in melting peaks. Therefore, introduction of calcium silicate whisker into polyamide induces the increase of crystallinity, effect of which is more pronounced within the range of critical whisker content.
Sample PA1012 PAC-10 PAC-20 PAC-30 PAC-40 ΔHc(J/g) 43.1 47.8 48.5 44.7 43.2 Table 2. ΔHc of pure PA1012 and its nanocompositesThermal Stability
The use of nanoclay has been attracted great attention in recent years to improve the thermal stability of polymer. For example, in ternary composite iPP/OMMT/PEOc, a compact and stable three-dimensional network was confirmed, effectively increasing thermal stability[35]. For our research, Fig. 7(a) shows thermal gravimetric analysis for PA1012 as well as its nanocomposites, from which the onset degradation temperature, listed in Table 3, is derived. It can be seen that the nanocomposites, as a two phase system, possess better thermal stability than pure PA1012 evaluated by onset temperature of degradation. Among them, the nanocomposite containing 10 wt% whiskers raises 10 K in comparison with pure polyamide. Moreover, the weight fraction of whiskers can be deduced from the final plateau value which is in agreement with the value in the mixing process, implying the loss of whiskers in the preparation procedure can be ignored.
Sample PA1012 PAC-10 PAC-20 PAC-30 PAC-40 Tonset(℃) 447.2 456.4 456.7 458.3 460.6 Tviscat(℃) 156 164 166 170 174 Table 3. The onset temperature of thermal gravity and Viscat softening temperatureFigure 7(b) shows deformation as a function of temperature of pure PA1012 and its composites and Viscat softening temperatures are listed in Table 3. Apparently, the Viscat softening temperature increases significantly with increase content of whiskers, which is closely correlated with high modulus described in mechanical properties part. Among which, the Viscat softening temperature of PAC-10 is 164 ℃, which is 8 ℃ higher than neat polyamide. From the stated above, it can be confirmed that the calcium silicate whisker effectively increases thermal stability of polyamide due to its perfect structure and its strong interaction with polyamide matrix.
Water Absorption of PA1012/Calcium Silicate Whisker and Its Influence in Mechanical Properties
Specimens prepared for tensile, flexural and impact tests are involved in water uptake test indicated in Fig. 5 and the corresponding mechanical properties of these specimens are summarized in Table 1. Water absorption of neat PA1012 and nanocomposites are shown in Fig. 5. With hydrogen bonding in polymer chain, neat polyamide tends to have higher water absorption as shown in Fig. 5. The water absorption of the calcium silicate whisker is hard to be detected due to its fluffy needle-like shape, but it definitely shares higher water absorption than neat polyamide. From this aspect, the water absorption of the PA1012 in the nanocomposites should be even lower than that shown in Fig. 5. Therefore, in this research, the water absorption of PA1012 in the nanocomposites, which is generally evaluated by the total water absorption of nanocomposites, is reasonable. The water absorption seriously influenced mechanical properties (revealed in Table 1). For example, for flexural specimens, a 50.4% reduction was found with 1.25% water uptake. This is probably ascribed to the fact that hydrogen bonds, intrinsically existed in polyamide chains, are destroyed by water attachment[34]. As expected, the impact strength improves a lot as a consequence of the plasticization of water in polyamide matrix. For PA1012/calcium silicate whisker composites, the water absorption is lower than that of neat PA1012. This may originate from the fact that the homogenously dispersed calcium silicate whisker intercalates in polyamide, which becomes a barrier of water molecules to pass through matrix. Moreover, as for polyamide, the hydrogen bonding formation with whiskers reduces the possible interaction with water molecule to some extent. Considering water sorption of polyamide, another important factor lies in the amorphous region because water is attracted only in the amorphous part[3]. As will be discussed in the latter section about melting behaviors, the degree of crystallinity of nanocomposites increases to some extent suggesting closer stacking of the molecular chains, in other words, the amorphous fraction reduces which may also decrease water permeability. In addition, for nanocomposites, a 38.6% reduction of flexural strength, less than 50.4% mentioned in neat PA1012, is observed with 1.07% water uptake. From this comparison, the incorporation of calcium silicate whisker into PA1012 not only improves the matrix mechanical properties but also increases its water resistance.
Table 1. Comparison of mechanical properties of pure PA1012 and PAC-20 with specimens after water absorption tests
Mechanical properties Tensile properties Flexural properties Impact property Break strength (MPa) Tensile modulus (MPa) Bending strength (MPa) Bending modulus (MPa) Impact strength (kJ/m2) PA1012 48.7±1.7 566.0±12.0 38.7±0.3 963.0±34.2 6.37±0.8 PA1012-w 41.9±1.3 239.7±6.7 19.2±0.2 461.7±5.9 15.1±1.2 PAC-20 55.4±0.6 1009.0±32.0 57.7±0.4 1801.2±87.1 4.67±0.2 PAC-20-w 44.5±1.1 528.2±10.2 35.0±0.2 1070.3±18.3 5.30±0.5 Table 1. Comparison of mechanical properties of pure PA1012 and PAC-20 with specimens after water absorption testsCONCLUSIONS
PA1012/calcium silicate whisker nanocomposites, without any coupling agent, were simply prepared by a twin-extruder method and superior mechanical and thermal properties were obtained. Through the research of morphology, homogenous dispersion in transverse direction and well oriented microstructure in longitudinal direction of injection molded nanocomposites, even in high whisker content, were given which was of great importance to the enhancement of mechanical properties. The essence of the higher efficiency of reinforcement was put forward that strong interaction of two components plays a significant role, resulting from hydrogen bonding interaction between carbonyl group in polyamide chain and hydroxyl group in whisker surface as well as large surface area of whiskers. Through this, a satisfied stress-transfer was realized in the nanocomposites. It was also found that the optimal performance, considering the balance of strength and toughness, could be reached when the whisker content was less than 20 wt%. What’s more, the results of water absorption and its effect on the mechanical performance confirmed that incorporation of calcium silicate whisker into PA1012 could not only improve the mechanical properties but also develop the water barrier properties, which was intensively associated with physical performance. This was probably due to the fact that the needle-like shape whisker, intercalated in polyamide matrix, became a barrier of water permeation as well as the reduced fraction of amorphous part revealed by thermal behaviors. As expected, thermal stability was raised a lot showing increase of the onset temperature of degradation and Viscat softening temperature. In conclusion, calcium silicate whisker is a perfect alternative in reinforcement of PA1012, which could be well dispersed in matrix even under high filler content, and prepare nanocomposites with superior mechanical and thermal properties.
-
-
[1]
Ou, Y.C., Yang, F. and Chen, J., J. Appl. Polym. Sci., 1997, 64(12):2317 doi: 10.1002/(ISSN)1097-4628
-
[2]
Abad, M.J., Ares, A., Noguerol, R., Garcia, X., Cerecedo, C., Valcarcel, V., Caamano, J.M. and Guitian, F., Polym. Compos., 2012, 33(12):2207 doi: 10.1002/pc.22364
-
[3]
Tjong, S.C. and Meng, Y.Z., Polymer, 1999, 40(5):1109 doi: 10.1016/S0032-3861(98)00340-1
-
[4]
Tjong, S.C. and Meng, Y.Z., Polymer, 1998, 39(22):5461 doi: 10.1016/S0032-3861(97)10294-4
-
[5]
Li, L.J. and Yang, G.S., J. Appl. Polym. Sci., 2010, 115(6):3376 doi: 10.1002/app.v115:6
-
[6]
Logakis, E., Pandis, C., Peoglos, V., Pissis, P., Stergiou, C., Pionteck, J., Potschke, P., Micusik, M. and Omastova, M., J. Polym. Sci., Part B:Polym. Phys., 2009, 47(8):764 doi: 10.1002/polb.v47:8
-
[7]
Ben Elmabrouk, A., Thielemans, W., Dufresne, A. and Boufi, S., J. Appl. Polym. Sci., 2009, 114(5):2946 doi: 10.1002/app.v114:5
-
[8]
Loos, M.R., Abetz, V. and Schulte, K., Macromol. Chem. Phys., 2011, 212(12):1236 doi: 10.1002/macp.v212.12
-
[9]
Ljungberg, N., Cavaille, J.Y. and Heux, L., Polymer, 2006, 47(18):6285 doi: 10.1016/j.polymer.2006.07.013
-
[10]
Tjong, S.C. and Jiang, W., Polym. Compos., 1999, 20(6):748 doi: 10.1002/(ISSN)1548-0569
-
[11]
Bahar, E., Ucar, N., Onen, A., Wang, Y.J., Oksuz, M., Ayaz, O., Ucar, M. and Demir, A., J. Appl. Polym. Sci., 2012, 125(4):2882 doi: 10.1002/app.v125.4
-
[12]
Liu, T.X., Chen, D., Phang, I.Y. and Wei, C., Chinese J. Polym. Sci., 2014, 32(1):115 doi: 10.1007/s10118-014-1383-3
-
[13]
Yu, M., Zhang, Q. and Fu. Q., Chinese J. Polym. Sci., 2003, 41(22):43
-
[14]
Shi, J., Wang, Y., Li, Y.L. and Wu, J., Chinese J. Polym. Sci., 2009, 27(5):703 doi: 10.1142/S0256767909004400
-
[15]
Ben Mabrouk, A., Vilar, M.R., Magnin, A., Belgacem, M.N. and Boufi, S., J. Colloid Interf. Sci., 2011, 363(1):129 doi: 10.1016/j.jcis.2011.07.050
-
[16]
Baschek, G., Hartwig, G. and Zahradnik, F., Polymer, 1999, 40(12):3433 doi: 10.1016/S0032-3861(98)00560-6
-
[17]
Miri, V., Persyn, O., Lefebvre, J.M. and Seguela, R., Eur. Polym. J., 2009, 45(3):757 doi: 10.1016/j.eurpolymj.2008.12.008
-
[18]
Launay, A., Marco, Y., Maitournam, M.H. and Raoult, I., Mech. Mater., 2013, 56:1 doi: 10.1016/j.mechmat.2012.08.008
-
[19]
Ali, M.A., Tateyama, S., Oka, Y.; Kaneko, D., Okajima, M.K. and Kaneko, T., Macromolecules, 2013, 46(10):3719 doi: 10.1021/ma400395b
-
[20]
Wurm, A., Ismail, M., Kretzschmar, B., Pospiech, D. and Schick, C., Macromolecules, 2010, 43(3):1480 doi: 10.1021/ma902175r
-
[21]
Sun, T.C., Chen, F.H., Dong, X. and Han, C.C., Polymer, 2008, 49(11):2717 doi: 10.1016/j.polymer.2008.04.021
-
[22]
Yuan, Z.K., Yu, J.H., Rao, B.L., Bai, H., Jiang, N., Gao, J. and Lu, S.R., Macromol. Res., 2014, 22(4):405 doi: 10.1007/s13233-014-2049-2
-
[23]
Ares, A., Lasagabaster, A., Abad, M.J., Noguerol, R., Cerecedo, C., Valcarcel, V., Caamano, J.M. and Guitian, F., J. Compos. Mater., 2014, 48(25):3141 doi: 10.1177/0021998313507615
-
[24]
Ben Mabrouk, A., Kaddami, H., Magnin, A., Belgacem, M.N., Dufresne, A. and Boufi, S., Polym. Eng. Sci., 2011, 51(1):62 doi: 10.1002/pen.v51.1
-
[25]
Palaniyandi, V. and Simonsen, J., Compos. Interface, 2007, 14(1):73 doi: 10.1163/156855407779230308
-
[26]
Sato, H., Sasao, S., Matsukawa, K., Kita, Y., Yamaguchi, H., Siesler, H.W. and Ozaki, Y., Macromol. Chem. Phys., 2003, 204(10):1351 doi: 10.1002/macp.200390108
-
[27]
Scaffaro, R. and La Mantia, F.P., Macromol. Chem. Phys., 2006, 207(3):265 doi: 10.1002/(ISSN)1521-3935
-
[28]
Dencheva, N., Denchev, Z., Oliveira, M.J. and Funari, S.S., Macromolecules, 2010, 43(10):4715 doi: 10.1021/ma100071e
-
[29]
Majumdar, B., Keskkula, H. and Paul, D.R., Polymer, 1994, 35(7):1399 doi: 10.1016/0032-3861(94)90339-5
-
[30]
Li, R., Xiong, C.X., Kuang, D.L., Dong, L.J., Lei, Y.A., Yao, J.L., Jiang, M. and Li, L.B., Macromol. Rapid Commun., 2008, 29(17):1449 doi: 10.1002/marc.v29:17
-
[31]
Yoo, Y., Cui, L., Yoon, P.J. and Paul, D.R., Macromolecules, 2010, 43(2):615 doi: 10.1021/ma902232g
-
[32]
Kang, M., Myung, S.J. and Jin, H.J., Polymer, 2006, 47(11):3961 doi: 10.1016/j.polymer.2006.03.073
-
[33]
Essawy, H.A., Badran, A.S., Youssef, A.M. and Abd El Haki, A.E.A., Macromol. Chem. Phys., 2004, 205(17):2366 doi: 10.1002/(ISSN)1521-3935
-
[34]
Haggenmueller, R., Du, F.M., Fischer, J.E. and Winey, K.I., Polymer, 2006, 47(7):2381 doi: 10.1016/j.polymer.2006.01.087
-
[35]
Sun, T.C., Dong, X., Du, K., Wang, K., Fu, Q. and Han, C.C., Polymer, 2008, 49(2):588 doi: 10.1016/j.polymer.2007.11.033
-
[1]
-

计量
- PDF下载量: 0
- 文章访问数: 742
- HTML全文浏览量: 66