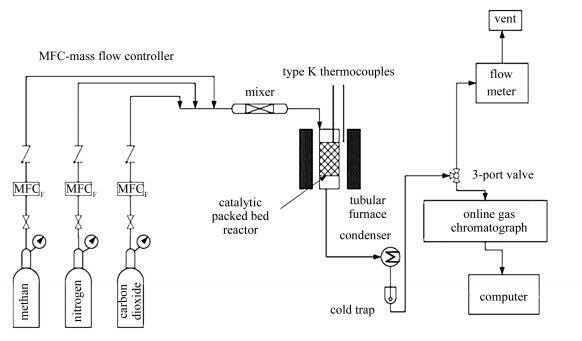

Citation: ZHANG Yu-bin, JING Jie-ying, LI Ting-yu, HUO Jun-mei, LI Wen-ying. Influence of preparation method on the structure of NiCo/MgO catalyst and its performance in the reforming of CH4 with CO2[J]. Journal of Fuel Chemistry and Technology, 2017, 45(7): 846-853.

制备方法对NiCo/MgO催化剂结构及其甲烷二氧化碳重整反应性能的影响
English
Influence of preparation method on the structure of NiCo/MgO catalyst and its performance in the reforming of CH4 with CO2
-
Key words:
- methane reforming with CO2
- / preparation method
- / Ni
- / Co
- / MgO
- / deposition-precipitation
- / co-precipitation method
- / co-impregnation
-
甲烷二氧化碳重整(CH4-CO2重整)制合成气在有效利用天然气、能量传输和解决日益严重的环境问题方面具有广阔的应用前景[1-3]。但CH4-CO2重整制合成气的反应条件恰处于热力学积炭区,开发高效稳定且高抗积炭性能的催化剂是该过程工业化的一个关键问题。目前,大量研究集中在贵金属和镍(Ni)基催化剂[4-6],前者价格昂贵,后者因积炭严重稳定性差。
近年来,研究者通过对Ni基催化剂改性来达到增强抗积炭性能的目的[7-9]。双金属催化剂由于其可调变的物理化学性质,双金属间的电子效应和几何效应,而表现出不同于单金属催化剂的独特性质和优异的催化性能。相比于贵金属(如Pt、Au)[10-12],非贵金属(如Co, Fe)[13-15]掺杂由于其价格优势而成为研究热点。由于NiO、CoO与MgO晶格参数相近,可以形成固溶体,使活性金属与载体间具有很强的相互作用,还原后得到高分散度的活性金属[16-19]。然而,即便是相同的活性组分,制备方法的差异会影响活性组分的还原性、粒径、分散度以及催化剂的微观结构,进而引起催化剂反应活性和选择性的明显不同,而且在抗积炭能力方面也有显著差异[20-24]。
课题组前期采用分步浸渍法成功制备了NiCo/MgO催化剂[25],为了进一步提高活性金属的还原性,同时使活性组分更均匀地分散在载体上,选择一种常用于制备高分散贵金属催化剂的沉积沉淀法[26-28]制备NiCo/MgO催化剂。
本研究采用沉积沉淀法、共沉淀法和共浸渍法,在相同干燥、焙烧和还原条件下,制备了Ni、Co质量分数为10%的NiCo/MgO催化剂(其中, Ni负载量为8%,Co负载量为2%,通过ICP-MS、XRD、H2-TPR、BET、TG等现代仪器分析表征技术对催化剂结构进行表征分析,结合催化剂活性评价实验,考察了制备方法对NiCo/MgO催化剂结构及其甲烷二氧化碳重整反应性能的影响。
1 实验部分
1.1 催化剂的制备
1.2 催化剂的表征
采用电感耦合等离子体发射光谱(ICP-MS)测定催化剂样品中各元素的含量。样品需先经消解和稀释配置成待测溶液。消解处理过程如下:称量0.05 g样品放置于聚四氟乙烯消解罐中,向样品中加入消解液(1 mL质量分数40% HF + 1 mL 30% H2O2 + 4 mL 14.4 mol/L HNO3),密封好消解罐并于微波消解仪中加热进行消解。消解得到的液体加入去离子水稀释配制成待测溶液。利用ICP-MS测定待测溶液中金属离子Ni2+、Co2+、Mg2+的含量,每种样品做三次平行实验。
催化剂晶相结构采用日本理学Rigaku D/Max -3B型X射线衍射仪(X-ray Diffraction,XRD)进行分析。其中,辐射源为Cu靶Kα射线(λ=0.154 nm),管电压为40 kV,管电流为100 mA,扫描速率为8(°)/min,35°-90°扫描。实验前催化剂在800 ℃下,采用50 mL/min 10% H2/Ar(体积比)混合气还原1 h。
催化剂的还原性在Autochem Ⅱ2920化学吸附仪(美国Micromeritics公司)上通过氢气程序升温还原(H2 Temperature Program Reduction,H2-TPR)实验进行研究。具体操作过程如下:将0.02 g催化剂置于石英U型管中,在50 mL/min Ar气氛下升温至200 ℃,恒温处理30 min后降至25 ℃,待基线平稳后将气体切换为50 mL/min 10% H2/Ar(体积比)混合气,以10 ℃/min升温至900 ℃。
催化剂表面活性金属的分散度在Autochem Ⅱ2920化学吸附仪(美国Micromeritics公司)上通过氢气程序升温还原(H2 Temperature Program Reduction,H2-TPR)实验测定。具体操作过程如下:实验前催化剂在800 ℃下,采用50 mL/min 10% H2/Ar(体积比)混合气还原1 h。取0.05 g还原后的催化剂置于石英U型管中,在50 mL/min Ar气氛中升温至400 ℃并保持1 h,然后切换成10% H2/Ar(体积比)混合气还原20 min,以避免空气氧化的影响及除去表面吸附的杂质气体。在Ar气氛中降温至50 ℃,然后切换成50 mL/min 10% H2/Ar(体积比)混合气脉冲进样,进样环容量为0.5 mL,直至吸附饱和,由Autochem Ⅱ2920化学吸附仪记录H2吸附量。
催化剂的比表面积和孔结构采用JW-BK122W型物理吸附仪(精微高博)测试。测试前将催化剂在200 ℃抽真空状态下预处理2 h,脱除吸附的水、空气等杂质。采用BET法计算催化剂的比表面积,针对吸附-脱附曲线中脱附数据采用BJH模型计算孔径分布。
反应后催化剂表面的积炭量采用HCT-1热重分析仪(北京恒久)进行测试。以30 mL/min空气为氧化气,温度从室温以10 ℃/min升温至1 000 ℃,参比为空Al2O3坩埚,样品用量为30 mg。
1.3 催化剂的活性评价
催化剂的活性评价在固定床反应器(装置示意图见图 1)中进行。采用内径为13 mm,长度为400 mm的石英玻璃管为反应器,催化剂粒径为0.25-0.35 mm,装填量为0.2 g。反应前,催化剂在800 ℃下,采用50 mL/min 10% H2/Ar(体积比)混合气还原1 h,而后切换至反应气体,实验条件为:800 ℃,0.1 MPa,CH4和CO2流量均为60 mL/min,空速为36 000 mL/(g·h)。反应后的气体组成由海欣气相色谱仪(碳分子筛填充柱TDX-01,TCD检测器)进行检测,色谱各区域温度条件为:柱炉温度为70 ℃,汽化温度为120 ℃,检测温度为150 ℃,热导温度为70 ℃。转化率和收率指标按以下计算公式给出:
转化率:
收率:
式中,Fx, in和Fx, out分别表示CH4、CO2、H2、CO各气体在反应器进、出口的体积流量,下标x指代相应物种,xCH4、xCO2分别表示CH4和CO2的转化率,wH2、wCO分别表示H2和CO的收率。
1.1.1 沉积沉淀法制备NiCo/MgO催化剂
称取0.79 g Ni(NO3)2·6H2O和0.19 g Co(NO3)2·6H2O溶解于20 mL去离子水中,充分搅拌溶解后得到溶液A;将0.82 g CO(NH2)2溶解于60 mL去离子水中,搅拌均匀后得到溶液B;向溶液A中加入2 g MgO(Aldrich,AR),搅拌均匀得到溶液C;将溶液B加入溶液C中,调节滴加速率保证混合体系的pH值维持在10左右,滴加完毕后,保持混合体系在90 ℃下继续搅拌2 h;将得到的产物采用去离子水抽滤洗涤,至滤液呈中性为止。然后将其放入干燥箱中120 ℃加热干燥24 h,冷却后于马弗炉中600 ℃焙烧6 h,即得试样,记做DP。
1.1.3 共浸渍法制备NiCo/MgO催化剂
称取0.79 g Ni(NO3)2·6H2O和0.19 g Co(NO3)2·6H2O溶解于6 mL去离子水中,充分搅拌溶解后,向其中加入2 g MgO(Aldrich,AR),于室温下搅拌至干。然后将所得产物放入干燥箱中120 ℃加热干燥24 h,冷却后于马弗炉中600 ℃焙烧6 h,即得试样,记做CI。
1.1.2 共沉淀法制备NiCo/MgO催化剂
称取0.79 g Ni(NO3)2·6H2O、0.19 g Co(NO3)2·6H2O和12.82 g Mg(NO3)2·6H2O溶解于100 mL去离子水中,充分搅拌溶解后得到混合盐溶液;将5.51 g Na2CO3溶解于200 mL去离子水中,在60 ℃水浴条件下将上述混合盐溶液逐滴加入Na2CO3溶液中,过程中使用2 mol/L NaOH水溶液调节pH值,通过控制滴加量使溶液pH值维持在10左右。反应结束后,继续搅拌1 h,然后将得到的沉淀物在60 ℃老化18 h,采用去离子水抽滤洗涤沉淀物,至滤液呈中性为止。然后将所得产物放入干燥箱中120 ℃加热干燥24 h,冷却后于马弗炉中600 ℃焙烧6 h,即得试样,记做CP。
2 结果与讨论
2.1 不同制备方法催化剂的元素组成
表 1为不同制备方法NiCo/MgO催化剂的元素组成。由表 1可知,各催化剂中Ni、Co双金属的质量分数为10%,且Ni/Co比为4,表明不同制备方法均可保证活性组分Ni、Co按照添加量及添加比例负载于MgO载体上。
表 1 不同制备方法NiCo/MgO催化剂的元素组成 Table 1. Element composition of the NiCo/MgO catalysts synthesized by different methods
2.2 不同制备方法催化剂的晶相结构
不同制备方法催化剂在800 ℃下,采用50 mL/min 10% H2/Ar(体积比)混合气还原1 h后进行XRD测试。图 2为还原后NiCo/MgO催化剂的XRD谱图。由图 2可知,74.6°、78.5°处的特征衍射峰表示NiO、CoO与MgO形成了固溶体。同时可以看到,使用沉积沉淀法和共沉淀法制备NiCo/MgO催化剂出现了Ni、Co金属单质的衍射峰,但使用共浸渍法制备的催化剂并没有呈现Ni、Co金属单质的衍射峰,这与催化剂的还原性密切相关,可能是由于共浸渍法制备的催化剂所能还原出的Ni、Co量太少,低于XRD的检测下限。采用Scherrer公式计算Ni/Co金属颗粒粒径,沉积沉淀法和共沉淀法制备的NiCo/MgO催化剂中金属颗粒粒径分别为6.1和11.6 nm。由于三种催化剂(DP、CP、CI)中Ni、Co双金属的含量基本相同(表 1),则沉积沉淀法制备的DP催化剂因其颗粒粒径小,能提供更多的活性面,从而有利于催化剂活性的提高。
2.3 不同制备方法催化剂的还原性
图 3为不同制备方法催化剂的H2-TPR谱图。由图 3可知,三种催化剂在200-400 ℃、400-600 ℃、600-900 ℃均有还原峰,但还原峰位置和大小不同,说明不同制备方法会导致催化剂的还原性具有明显差异。在200-400 ℃观察到DP、CP催化剂具有明显的还原峰,表明其载体MgO表面存在自由或游离的NiO或CoO[25];在400-600 ℃,DP、CP和CI催化剂均具有明显的还原峰,表明三种催化剂表面存在NiO或CoO,且与载体MgO有一定的相互作用力;在600-900 ℃,DP、CP催化剂具有归属于NiO/CoO-MgO固溶体中NiO或CoO的还原峰,表明其与载体具有较强的金属-载体相互作用,经还原后可得到更为稳定的Ni、Co物种,可有效防止活性组分Ni、Co的烧结,有利于提高催化剂的稳定性[29]。
由H2-TPR原理可知,在相同还原条件下,还原峰面积大小与被还原物种的含量成正比。由图 3还可知,DP催化剂中600-900 ℃还原峰的相对面积大于200-600 ℃还原峰的相对面积;CP催化剂中200-600 ℃还原峰的相对面积明显大于600-900 ℃还原峰的相对面积;而CI催化剂的还原峰主要集中在400-600 ℃,且相对面积较小。比较三种催化剂可以发现,DP催化剂中NiO/CoO-MgO固溶体的还原峰相对面积比例最大,表明还原后可得到更多稳定性较好的活性组分Ni和Co。同时,根据整体还原峰的面积大小可得到三种催化剂的还原性排序为CP > DP > CI。
2.4 不同制备方法催化剂的活性金属分散度与颗粒粒径
采用H2脉冲吸附实验测定还原后的NiCo/MgO催化剂金属分散度和颗粒粒径,结果见表 2。由表 2可知,DP催化剂的活性金属比表面积(7.0 m2/g)、分散度(10.4%)明显大于CP和CI催化剂,且DP催化剂中活性金属粒径最小(9.7 nm)。这是因为,共浸渍法制备的CI催化剂还原性很差,导致还原出的活性金属量很少,且其金属分散度最差(3.7%),使得金属粒径大(26.9 nm)。虽然使用共沉淀法制备的CP催化剂还原性大于沉积沉淀法制备的DP催化剂,其还原出的活性金属量大,但CP催化剂还原后暴露出的活性金属比表面积小于DP催化剂,且金属分散度较差(7.9%),金属颗粒粒径较大(12.8 nm)。这是由于制备过程中沉积沉淀法使用尿素为沉淀剂,随着溶液温度的逐渐上升,达到尿素的水解温度,尿素逐渐在整个溶液中均匀的水解释放OH-,为Ni2+、Co2+的完全水解沉淀提供了碱性环境,粒子的成核和生长速率相对较快,不存在共沉淀法因使用NaOH和Na2CO3作为沉淀剂在逐渐滴加盐过程中的局部过饱和现象。因此,沉积沉淀法制备的DP催化剂中Ni2+、Co2+能够均匀的沉积沉淀在载体MgO表面,产生较小的金属颗粒,经还原后可以暴露更多的活性表面。
表 2 不同制备方法催化剂金属分散度与颗粒粒径 Table 2. Metal dispersion and particle size of the NiCo/MgO catalysts synthesized by different methods
2.5 不同制备方法催化剂的比表面积和孔结构
不同制备方法催化剂的比表面积及孔结构参数见表 3。由表 3可知,制备方法对催化剂的比表面积、孔体积、最可几孔径影响明显。相比于所用载体MgO的比表面积(70.2 m2/g),催化剂负载活性金属后,比表面积均呈下降趋势,其中,采用沉积沉淀法制备的DP催化剂比表面积最大(68.1 m2/g),有利于Ni、Co在其表面的分散;而共浸渍法制备的CI催化剂比表面积最小(42.9 m2/g)。这是由于在不同制备过程中,活性金属占据了不同数量的载体孔径较小的孔道,导致不同制备方法所得催化剂比表面积减小程度不同。对于共沉淀法制备的CP催化剂,制备过程中活性金属离子与Mg2+一起沉淀,其比表面积为61.2 m2/g。同时可以看到,各催化剂的最可几孔径为9-15 nm,属于介孔结构,表明不同方法所制备的催化剂均为介孔材料。
表 3 不同制备方法催化剂的比表面积和孔结构 Table 3. BET specific surface area and pore structure of the NiCo/MgO catalysts synthesized by different methods
2.6 不同制备方法催化剂的反应性能评价
在800 ℃,0.1 MPa,空速36 000 mL/(g·h)条件下考察三种制备方法催化剂的CH4-CO2重整反应性能。图 4、图 5是不同制备方法催化剂的CH4和CO2转化率,H2和CO的收率随反应时间的变化曲线。
由图 4、图 5可知,DP催化剂的活性和稳定性明显优于CP和CI催化剂,其催化活性为:DP > CP > CI。反应8 h内,DP催化剂的CH4和CO2转化率保持在88%和92%,接近800 ℃的热力学平衡转化率(CH4为90%、CO2为95%),这主要是因为采用沉积沉淀法制备的DP催化剂金属分散度好(10.4%),活性金属的还原度高,暴露在催化剂表面的活性位点较多,且活性金属颗粒粒径小(9.7 nm),使其表现出较高的活性;与此同时,DP催化剂中Ni/Co与MgO之间具有较强的相互作用,使其还原后稳定性好,能有效防止活性组分Ni/Co的烧结,从而使得DP催化剂表现出良好的稳定性。对于共沉淀法制备的CP催化剂,其初始CH4和CO2转化率分别为70%和84%,随着反应时间的延长,CP催化剂的CH4和CO2转化率不断增加,8 h后其CH4和CO2转化率分别为81%和90%。这是由于CP催化剂载体表面活性金属的分散不均匀造成的。结合H2-TPR(图 3)与H2脉冲吸附分析结果(表 2)可知,在反应初始阶段,CP催化剂暴露出的活性金属比表面积小于DP催化剂,金属分散度差(7.9%),金属颗粒粒径大(12.8 nm),导致其初始CH4和CO2转化率低于DP催化剂。随着反应的进行,在产物H2和CO的作用下,CP催化剂中原先未被还原出来的活性金属被不断的还原出来,使其催化活性逐渐提高。而采用共浸渍法制备的CI催化剂,由于其较低的还原性,导致其暴露在催化剂表面的活性位点较少,且在三种催化剂中,CI催化剂金属颗粒粒径最大(26.9 nm),活性金属分散度最差(3.7%),这些因素共同导致CI催化剂的初始CH4和CO2转化率分别仅为45%和59%。同时可以看到,DP催化剂的H2收率比CP、CI催化剂分别高约10%和43%,CO收率比CP、CI催化剂分别高约13%和42%,且稳定性更好。
为了进一步考察不同制备方法催化剂的抗积炭性能,对反应后的催化剂进行了热重分析。由TGA结果(图 6)可知,使用沉积沉淀法制备的DP催化剂反应后的积炭量(1.2%,质量分数)明显小于其他两种方法(CP催化剂2.2%,CI催化剂2.8%)。结合H2脉冲吸附分析结果(表 2)可以发现,随着活性金属颗粒粒径的减小,三种催化剂的积炭量相应减小。
由图 6可知,DP催化剂在350-500 ℃出现了一个明显的增重峰,这是由于沉积沉淀法制备的DP催化剂积炭量较小,活性金属在空气中被氧化引起的。通常文献认为,积炭产生需要的金属颗粒粒径大于CH4-CO2重整反应所需要的金属颗粒粒径,在小于临界粒径的金属颗粒上,积炭生成的速率显著降低[30]。采用沉积沉淀法制备的DP催化剂具有较高的活性金属分散度,使其暴露在催化剂表面的活性位点较多,且活性金属颗粒粒径较小(9.7 nm),提高了催化剂的抗积炭性能和催化活性。
3 结论
催化剂的制备方法对活性金属质量分数相同(10%)的NiCo/MgO催化剂的还原性、活性金属粒径、分散度和比表面积等均有很大影响,进而引起了NiCo/MgO催化剂的CH4-CO2重整反应性能差异。沉积沉淀法制备的DP催化剂金属粒径小、分散度高、比表面积大,从而催化剂的活性较高;同时,DP催化剂中Ni/Co与MgO之间存在较强的相互作用,使其还原后稳定性好,能有效防止活性组分Ni/Co的烧结,有利于催化剂稳定性的提高。可见,沉积沉淀法是一种适合于制备高活性非贵金属负载型催化剂的有效方法。
-
-
[1]
FENG X, FENG J, LI W. CO2 reforming of CH4 over a highly active and stable ni-mg-al catalyst[J]. Int J Hydrogen Energy, 2017, 42(5): 3036-3042. doi: 10.1016/j.ijhydene.2016.09.205
-
[2]
FENG J, DING Y, GUO Y, LI X, LI W. Calcination temperature effect on the adsorption and hydrogenated dissociation of CO2 over the NiO/MgO catalyst[J]. Fuel, 2013, 109(7): 110-115.
-
[3]
张盼艺, 郭芳, 许俊强, 陈志, 李军. 基于强抗积碳的CO2重整镍基催化剂的研究进展[J]. 硅酸盐学报, 2016,44,(4): 620-626. ZHANG Pan-yi, GUO Fang, XU Jun-qiang, CHEN Zhi, LI Jun. Progress of coke resistant ability research of Ni-based catalysts for CO2 reforming of methane[J]. J Chin Ceram Soc, 2016, 44(4): 620-626.
-
[4]
PAKHARE D, SPIVEY J. A review of dry (CO2) reforming of methane over noble metal catalysts[J]. Chem Soc Rev, 2014, 43(22): 7813. doi: 10.1039/C3CS60395D
-
[5]
王明智, 张秋林, 张腾飞, 王一茹. Ni基甲烷二氧化碳重整催化剂研究进展[J]. 化工进展, 2015,34,(8): 3027-3034. WANG Zhi-ming, ZHANG Qiu-lin, ZHANG Teng-fei, WANG Yi-ru. Advance in Ni-based catalysts for the carbon dioxide reforming of methane[J]. Chem Ind Eng Prog, 2015, 34(8): 3027-3034.
-
[6]
付晓娟, 曾尚红, 苏海全. 用于甲烷二氧化碳重整新型催化材料的研究进展[J]. 化工进展, 2012,31,(S1): 168-175. FU Xiao-juan, ZENG Shang-hong, SU Hai-quan. Advance in catalytic materials for CO2 reforming of methane:A review[J]. Chem Ind Eng Prog, 2012, 31(S1): 168-175.
-
[7]
RUCKENSTEIN E, HANG Hu Y. Role of support in CO2 reforming of CH4 to syngas over ni catalysts[J]. J Catal, 1996, 162(2): 230-238. doi: 10.1006/jcat.1996.0280
-
[8]
霍苗苗, 李琳, 赵欣, 张煜华, 李金林. 氮化SBA-16负载镍基催化剂的制备及其对甲烷二氧化碳重整反应的催化性能[J]. 燃料化学学报, 2017,45,(2): 172-181. HUO Miao-miao, LI Lin, ZHAO Xin, ZHANG Yu-hua, LI Jin-lin. Synthesis of ni-based catalysts supported on nitrogen-incorporated SBA-16 and their catalytic performance in the reforming of methane with carbon dioxide[J]. J Fuel Chem Technol, 2017, 45(2): 172-181.
-
[9]
王冰, 郭聪秀, 王英勇, 靳国强, 郭向云. Ni-Smx/SiC催化剂甲烷二氧化碳重整性能研究[J]. 燃料化学学报, 2016,44,(5): 587-596. WANG Bin, GUO Cong-xiu, WANG Ying-yong, JIN Guo-qiang, GUO Xiang-yun. Performance of Ni-Smx/SiC catalysts for CO2 reforming of CH4[J]. J Fuel Chem Technol, 2016, 44(5): 587-596.
-
[10]
WU H, LA Parola V, PANTALEO G, PULEO F, VENEZIA A, LIOTTA L. Ni-based catalysts for low temperature methane steam reforming:Recent results on Ni-Au and comparison with other bi-metallic systems[J]. Catalysts, 2013, 3(2): 563-583. doi: 10.3390/catal3020563
-
[11]
GARCIA-DIEGUEZ M, PIETA I S, HERRERA M C, LARRUBIA M A, ALEMANY L J. Improved Pt-Ni nanocatalysts for dry reforming of methane[J]. Appl Catal A:Gen, 2010, 377(1/2): 191-199.
-
[12]
FAN M-S, ABDULLAH A Z, BHATIA S. Catalytic technology for carbon dioxide reforming of methane to synthesis gas[J]. ChemCatChem, 2009, 1(2): 192-208. doi: 10.1002/cctc.v1:2
-
[13]
SHESHKOT F, SEROV Y M. Bimetallic systems containing Fe, Co, Ni, and Mn nanoparticles as catalysts for the hydrogenation of carbon oxides[J]. Russ J Phys Chem A, 2012, 86(2): 283-288. doi: 10.1134/S0036024412020264
-
[14]
ZHANG F, WANG N, YANG L, LIM , HUANG L. Ni-Co bimetallic mgo-based catalysts for hydrogen production via steam reforming of acetic acid from bio-oil[J]. Int J Hydrogen Energy, 2014, 39(32): 18688-18694. doi: 10.1016/j.ijhydene.2014.01.025
-
[15]
MIRZAEI F, REZAEI M, MESHKANI F. Coprecipitated Ni-Co bimetallic nanocatalysts for methane dry reforming[J]. Chem Eng Technol, 2014, 37(6): 973-978. doi: 10.1002/ceat.v37.6
-
[16]
ZHANG J, WANG H, DALAI A K. Development of stable bimetallic catalysts for carbon dioxide reforming of methane[J]. J Catal, 2007, 249(2): 300-310. doi: 10.1016/j.jcat.2007.05.004
-
[17]
ZHANG J, WANG H, DALAI A K. Effects of metal content on activity and stability of Ni-Co bimetallic catalysts for CO2 reforming of CH4[J]. Appl Catal A:Gen, 2008, 339(2): 121-129. doi: 10.1016/j.apcata.2008.01.027
-
[18]
XU J, ZHOU W, LI Z, WANG J, MA J. Biogas reforming for hydrogen production over nickel and cobalt bimetallic catalysts[J]. Int J Hydrogen Energy, 2009, 34(16): 6646-6654. doi: 10.1016/j.ijhydene.2009.06.038
-
[19]
WANG Z, WANG C, CHEN S, LIU Y. Co-Ni bimetal catalyst supported on perovskite-type oxide for steam reforming of ethanol to produce hydrogen[J]. Int J Hydrogen Energy, 2014, 39(11): 5644-5652. doi: 10.1016/j.ijhydene.2014.01.151
-
[20]
莫, 马, 刘, 刘, 钟, 艾沙·努拉洪. 制备方法对Ni-Al2 O3催化剂在CO2-CH4重整反应中催化性能的影响[J]. 燃料化学学报, 2015,43,(9): 1083-1091. MO, MA, LIU, LIU, ZHONG, AISHA·Nulahong. Effect of preparation methods on the catalytic performance of Ni-Al2O3 for CO2-CH4 reforming[J]. J Fuel Chem Technol, 2015, 43(9): 1083-1091.
-
[21]
索掌怀, 徐秀峰, 马华宪, 安立敦. 制备方法对Ni/MgO/Al2O3在甲烷与二氧化碳重整反应中催化性能的影响[J]. 催化学报, 2000,21,(5): 411-414. SUO Zhang-huai, XU Xiu-feng, MA Hua-xian, AN Li-dun. Influence of preparation methods on catalytic performance of Ni/MgO/Al2O3 in CO2 reforming of CH4 [J]. Chin J Catal, 2000, 21(5): 411-414.
-
[22]
徐军科, 任克威, 周伟, 王晓蕾, 李兆静, 潘相敏, 马建新. 制备方法对甲烷干重整催化剂Ni/La2O3/Al2O3结构及性能的影响[J]. 燃料化学学报, 2009,37,(4): 473-479. XU Jun-ke, REN Ke-wei, ZHOU Wei, WANG Xiao-lei, LI Zhao-jing, PAN Xiang-min, MA Jian-xin. Influence of preparation method on the properties and catalytic performance of Ni/La2O3/Al2O3 catalyst for dry reforming of methane[J]. J Fuel Chem Technol, 2009, 37(4): 473-479.
-
[23]
CHEN L, ZHU Q, WU R. Effect of Co-Ni ratio on the activity and stability of Co-Mi bimetallic aerogel catalyst for methane oxy-CO2 reforming[J]. Int J Hydrogen Energy, 2011, 36(3): 2128-2136. doi: 10.1016/j.ijhydene.2010.11.042
-
[24]
FAN M S, ABDULLAH A Z, BHATIA S. Utilization of greenhouse gases through carbon dioxide reforming of methane over Ni-Co/MgO-ZrO2:Preparation, characterization and activity studies[J]. Appl Catal B:Environ, 2010, 100(1/2): 365-377.
-
[25]
HUO J, JING J, LI W. Reduction time effect on structure and performance of ni-co/mgo catalyst for carbon dioxide reforming of methane[J]. Int J Hydrogen Energy, 2014, 39(36): 21015-21023. doi: 10.1016/j.ijhydene.2014.10.086
-
[26]
KITTISAKMONTREE P, PONGTHAWORNSAKUN B, YOSHIDA H, FUJITA S I, ARAI M, PANPRANOT J. The liquid-phase hydrogenation of 1-heptyne over Pd-Au/TiO2 catalysts prepared by the combination of incipient wetness impregnation and deposition-precipitation[J]. J Catal, 2013, 297(1): 155-164.
-
[27]
SANDOVAL A, AGUIAR A, LOUIS C, TRAVERSE A, ZANELLA R. Bimetallic Au-Ag/TiO2 catalyst prepared by deposition-precipitation:High activity and stability in CO oxidation[J]. J Catal, 2011, 281(1): 40-49. doi: 10.1016/j.jcat.2011.04.003
-
[28]
PUTLURU S S R, SCHILL L, JENSEN A D, SIRET B, TABARIES F, FEHRMANN R. Mn/TiO2 and Mn-Fe/TiO2 catalysts synthesized by deposition precipitation-promising for selective catalytic reduction of NO with NH3 at low temperature[J]. Appl Catal B:Environ, 2015, 165: 628-635. doi: 10.1016/j.apcatb.2014.10.060
-
[29]
SIDIK S M, TRIWAHYONO S, JALILA A, MAJID Z A, SALAMUN N, TALIB N B, ABDULLAH T A T. CO2 reforming of CH4 over Ni-Co/MSN for syngas production:Role of Co as a binder and optimization using rsm[J]. Chem Eng J, 2016, 295: 1-10. doi: 10.1016/j.cej.2016.03.041
-
[30]
ROSTRUP-NIELSEN J R. Coking on nickel catalysts for steam reforming of hydrocarbons[J]. J Catal, 1974, 33(2): 184-201. doi: 10.1016/0021-9517(74)90263-2
-
[1]
-
表 1 不同制备方法NiCo/MgO催化剂的元素组成
Table 1. Element composition of the NiCo/MgO catalysts synthesized by different methods
表 2 不同制备方法催化剂金属分散度与颗粒粒径
Table 2. Metal dispersion and particle size of the NiCo/MgO catalysts synthesized by different methods
表 3 不同制备方法催化剂的比表面积和孔结构
Table 3. BET specific surface area and pore structure of the NiCo/MgO catalysts synthesized by different methods
-

计量
- PDF下载量: 0
- 文章访问数: 0
- HTML全文浏览量: 0